2021. 4. 3. 14:08ㆍ2001-적층세라믹 콘덴서의 개발과 재료기술 및 고신뢰성화
제2절 슬러리의 물성과 Sheet특성
서론
본 절에서는 적층 세라믹 콘덴서의 제조프로세스에서 슬러리에서 Sheet성형에 관계하는 기술에 대해 소개한다. 적층 세라믹 콘덴서의 제조공정은 여러 분야에 걸쳐 있으며, green sheet의 요구특성은 각각의 공정에 따라서 크게 변한다. 이 때문에 본 절에서는 일반적인 green sheet의 성형방법으로서, 닥터 블레이드(Dr. Blade)법을 중심으로, 슬러리 물성이 sheet 성형조건에 미치는 영향, 또한 green sheet의 특성에 미치는 영향에 대해서 설명하겠다.
1. 적층 세라믹 콘덴서에 요구되는 Sheet의 특성
고신뢰성, 고성능의 적층 세라믹 콘덴서를 안정하면서, 대량 생산하기위해서는 표1과 같은 세라믹 sheet가 필요하다. 최근에는 적층 세라믹 콘덴서의 박층화가 진행되고, green sheet의 품질에 대한 요구가 엄격해지고 있다. 특히, 유전체 3㎛이하의 적층 세라믹 콘덴서를 제조할 경우, 표면조도, Crator상 Pinhole등의 마이크로 결함들이 문제로 되어 왔다. 이들 green sheet의 결함은 먼지등의 부착뿐만 아니라 닥터 블레이드의 구조, sheet성형조건 및 세라믹 슬러리 조정조건으로부터 크게 영향을 받는다. 그림 1에 닥터 블레이드법에서 만들어진 green sheet의 각종 결함의 예를 나타내었다.
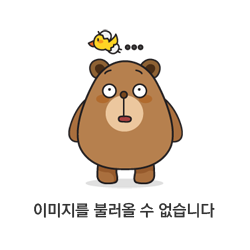
(1) orange peel
슬러리의 용제량 균형이 무너질 때에 관찰된다. 슬러리의 건조속도와 Levelling과 관계있다. 이같은 표면이 안 좋은 green sheet는 유전체층의 두께편차를 만들어 국부적인 전계 집중을 일으켜 IR 불량, 신뢰성저하의 원인이 된다.
(2) Crack
슬러리의 건조조건과 슬러리의 건조성이 원인이 되는 경우가 많다. 적층 세라믹 콘덴서의 cover층 등의 막 두께가 두꺼운 green sheet의 성형 시에 발생한다.
(3) 줄무늬
슬러리에 혼입된 이물질, 원료 분체의 응집체, binder의 미용해분 등에서 발생하고, 슬러리의 분산과 여과프로세스의 불안정함이 원인이 된다. 주름은 유전체층의 두께편차를 발생시키고, 국소적인 전계 집중을 발생시켜 IR 불량, 신뢰성 저하의 원인이 된다.
(4) Pinhole
슬러리에 혼입된 이물질이 튀어나가거나, 공기가 들어가서 생기는 Pore, film과의 wetting성에 의해 발생한다. Pinhole은 적층 세라믹 콘덴서의 Short불량에 직결하기 때문에 절대적으로 방지해야 한다
이들 sheet의 결함을 미연에 방지하는 것이 적층 세라믹 콘덴서의 신뢰성향상과 연결된다.
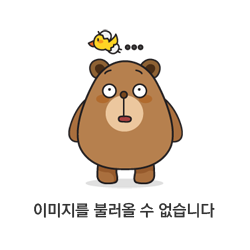
2. 슬러리조성
세라믹용의 슬러리 시스템으로서 수계와 용제계의 2종류로 분류된다. 수계 시스템은 공정비용이 작고, 환경 친화적인 것이 장점이나, 건조성과 wetting성이 문제로 되는 경우가 많다. 한편 용제계 시스템은 binder 및 용제, 첨가제등의 선택에 유연성이 있고, 또 건조성, 표면장력의 면에서 sheet성형이 용이하다는 장점이 있다. 적층 세라믹 콘덴서 제조공정은 양쪽 시스템 모두 사용되고 있으며, 어느 쪽의 시스템이 우수하다고 판단할 수 없지만, 프로세스 윈도우(process window) 가 넓은 용제계가 널리 쓰이고 있다. 그렇지만 최근 환경대책에 의해 용제계 시스템에 여러 가지 제약이 걸려 앞으로는 수계 바인더로 이행할 것이라 생각된다.
다음 적층 세라믹 콘덴서의 제조에 사용되는 슬러리에 대해서 설명한다. 세라믹용 슬러리는 주로 유전체재료, 바인더, 용제, 첨가제로 구성되어 있다. 표2에 세라믹용 슬러리의 구성재료와 기능에 대해서 나타내었다. 슬러리 조성의 설계에 있어서 표2에 표시된 구성재료의 배분이 green sheet의 물성을 결정하는데 중요하다.
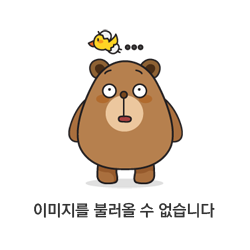
(1) 원료
원료인 유전체는 입도분포, 표면상태가 슬러리의 분산상태, 점도에 크게 영향을 준다.
(2) binder
바인더는 green sheet강도, 가소성, Tacky성 등에 영향을 주기 때문에 적층 세라믹 콘덴서의 요구특성에서 수지가 선택된다. 표3에 세라믹sheet성형에 사용되는 바인더의 종류와 일반적인 성질은 나타낸다.
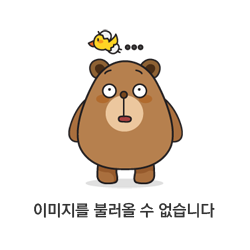
(3) 용제
용매는 크게 진용제, 희석용제로 나눌 수 있다. 진용제는 바인더를 용해하는 역할이고 , 슬러리의 주용매이다. 희석용제는 단독으로는 용해능력이 없는 빈 용매이고 슬러리의 건조제어, sheet조직의 제어를 위해서 첨가한다. 용제는 수지의 용해능력에서 선택되고 바인더를 혼합했을 때의 용해상태와 점도가 동시에 평가된다. 용해도 Parameter등을 참고해서 용제를 선택, blend 하는 경우도 있다. 또한 슬러리의 건조제어를 위해서. 다른 비점, 증기압의 용매를 혼합용매로 사용하는 경우도 있다. 세라믹 green sheet에 사용되는 용제로서 물, 알콜류, 톨루엔, 초산부틸, 시클로 헥산, MEK등이 사용된다.
(4) 첨가제
원료와 용제의 친화성 관점에서 분산제가 슬러리의 유동성, 표면장력의 개선을 위해 Wetting제를 첨가하는 경우가 있다. 분산제의 종류와 첨가량은 유전체분말과 용제의 친화성, 분산성, 슬러리 점도로부터 선택된다.
상기첨가제 이외에 sheet물성을 개선할 필요가 생길 경우 가소제, 이형제, 대전방지제등이 첨가된다. 이들 첨가제는 적층 세라믹 콘덴서에서 요구되는 sheet물성을 만족시키기 위해 첨가되는 경우가 많다.
(5) 가소제
수계시스템의 경우 글리세린등의 글리콜류가 사용된다. 용제계 시스템에서는 일반적으로 지방산 및 지방산 에스테르가 가소제로 사용된다.
(6) 이형제
일반적인 sheet공법의 적 프로세스에서는 green sheet를 film으로부터 박리하는 공정이 존재한다. green sheet의 박리는 통상 film에 Silicon수지 코팅을 실시하여 제어하지만, 박리성을 개선할 필요가 있을 경우 첨가한다.
(7) 대전방지제
green sheet 및 film의 박리 시에 정전기가 발생한다. 정전기의 발생은 적층시 주름의 발생, 주위의 먼지를 green sheet에 부착시키는 결함의 발생원인이 될 우려가 있다. 대전방지제는 이들 적층 프로세스 중에 발생하는 정전기의 발생을 감소시키기 위해 첨가된다. 일반적으로는 흡습성이 높은 고비점의 용제가 사용된다.
3. 슬러리화 PROCESS
슬러리화 PROCESS에는 유전체 분말, 바인더를 균일하게 분산시켜 성형공정에서 필요한 점도, 고형분 농도로 조정하는 공정이다. 그림 2에 일반적인 슬러리화 공정을 나타내었다.
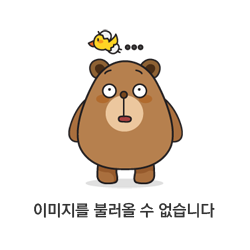
(1) 혼합-분산
혼합분산공정은 유전체분말을 균일하게 분산하는 공정으로, 이상적으로는 입자 하나하나를 단분산시키는 것이 중요하다. 이에 의해 코팅막내의 입자의 충진이 균일하게 되고, 막 표면의 평활성을 좋게 할 수 있다. 혼합분산공정은 유전체, 용제, 바인더와의 분산상태를 개선하기 위해서 예비분산처리나 투입순서 등의 연구가 필요하다. 혼합분산에 사용되는 분산기로서는, 볼밀을 사용할 경우와 고속교반기, 호모믹서, 샌드밀(비즈밀) 등을 병용하는 방법이 있다. 어떻게든 고분산 상태를 얻기 위해서 장치의 개량과 media의 소형화가 진행되고 있다.
(2) 조정
혼합분산공정을 끝낸 슬러리는 도포공정에 필요한 점도나 고형분을 조정하기 위해, 용제의 추가 첨가공정을 거치는 경우가 있다. 또, 혼합분산공정에서 발생한 열과 기포를 없애기 위해서 슬러리의 aging이나 탈포공정을 채용하고 있다.
(3) 여과
세라믹green sheet의 제조에 있어서, 슬러리 내의 이물질의 혼입이나 분산이 제대로 안되어 생긴 응집체, 미용해수지의 잔류는 Pinhole, crator, 주름의 발생 원인이 되어, 적층 세라믹 콘덴서의 신뢰성에 중대한 영향을 미친다. 이들의 발생을 미연에 방지하기 위해서, 혼합-분산처리후의 슬러리는 Filtering처리 후 sheet로 성형된다. Filtering공정에서는 수단계로 나누어 크기가 다른 이물질과 응집체를 잡아내는 구조를 취하고 있다.
4. 슬러리 물성과 Sheet막상태의 관계
슬러리의 물성, 주로 점도, 고형분 농도, 분산 조건에 대한 Sheet의 두께, 표면상태의 영향에 대해서 소개한다.
4.1 슬러리 점도와 성형막두께의 관계
슬러리 점도가 Sheet의 변화에 미치는 영향을 그림3에 나타내었다. 검토에 사용한 슬러리는 고형분농도 (비휘발분농도)를 일정하게 해서 건조 수축율이 일정하게 되도록 조정했다. 슬러리 점도가 증가할 수록 sheet두께는 감소되는 경향이 있다.
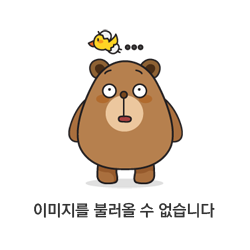
이 경향은 닥터 블레이드의 gap폭이 넓을 수록 현저하다. 이 특성은 슬러리 점도가 증가함에 따라서 닥터 블레이드의 gap로부터 슬러리의 자중에 의해 자연적으로 유출되는 슬러리의 양이 감소하기 때문이다. 한편 슬러리 점도를 용매량에 따라서 변화시킨 경우는, sheet두께는 용매의 건조수축이 지배적이고, 슬러리 점도와 sheet두께의 관계는 역전된다.
4.2 슬러리물성과 sheet표면상태의 관계
sheet표면상태는 적층 세라믹 콘덴서의 신뢰성에 큰 영향을 준다. 특히 크랙, pinhole, crator등의 sheet결함은 적층 세라믹 콘덴서의 short불량의 원인이 된다. 또, sheet의 표면조도는 박층화 시의 유전체층두께의 편차에 영향받고, 전계의 국부적인 집중이 일어나 IR불량, 신뢰성의 저하를 일으킨다. 여기서는 슬러리의 물성과 sheet의 표면상태의 관계에 대해서 소개한다.
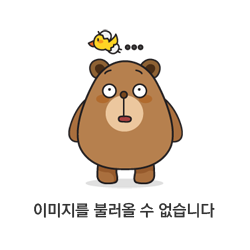
슬러리 분산시간과 표면조도의 관계를 그림4에 나타내었다. 슬러리 분산시간의 증가에 따라서, sheet표면조도는 감소한다. 이것은 유전체분말의 분산성이 개선됨에 따라 응집입자가 감소하고, Sheet중의 입자가 충진이 잘되기 때문이다.
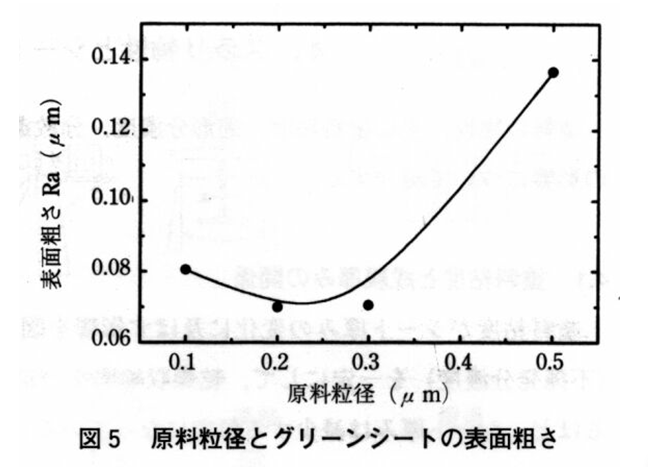
다음 그림5에 슬러리중의 원료입자경과 sheet표면조도의 관계를 나타내었다. 원료입경이 클수록 sheet의 표면조도가 증가하고 이것의 결과로부터 sheet 표면조도는 원료의 입경, 응집 상태 등에 의해서 영향을 받는다. (표4)
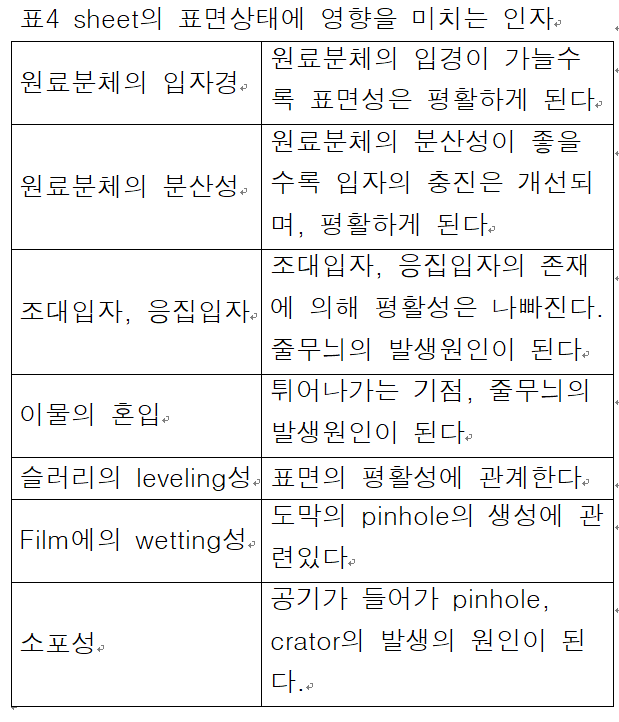
또 그림4 중에는 닥터 블레이드의 gap폭과 sheet표면조도의 관계도 표시했다. gap폭이 클수록 (sheet두께가 증가할수록) 표면조도가 감소하고 있다. 이것은 슬러리가 닥터 블레이드의 gap에서 유출한 sheet막 건조거동과 leveling특성에 관계되어 있다고 생각된다. sheet두께가 얇을수록 sheet막의 건조가 빠르게 되고, 슬러리의 leveling이 진행하기 어렵게 되기 때문에 표면조도가 증가한다고 예상된다. 이 때문에 박층용의 세라믹 green sheet를 성형할 경우는 슬러리 분산성과 건조제어, leveling제어가 중용하게 되었다. 특히 비점이 낮아, 건조속도가 빠른 용매를 많이 첨가한 경우 그림1에 나타낸 orange peel 현상이 나타난다. 이상과 같이, 닥터 블레이드법에 의한 green sheet의 표면상태는 슬러리의 분산상태, 슬러리의 점도특성, 슬러리의 건조수축거동에 크게 영향받는다.
그 외 green sheet의 표면상태를 결정하는 원인으로서는 슬러리의 레올로지특성을 들 수 있다. 일반적으로 도공부분 (닥터 블레이드, 롤과 film사이)에는 큰 전단응력이 걸리므로 슬러리가 비newton성을 나타내는 경우, 도막직후의 shear가 해방된 상태이어서 점도증가가 일어나고, sheet의 leveling가 저해되어 표면조도가 증가하는 경우가 있다.
5. sheet성형조건과 sheet상태의 관계
sheet성형에 따른 성형두께의 제어방법과 요인에 대해서 검토해 보았다. 닥터 블레이드의 gap폭과 sheet 두께의 관계를 상세하게 조사해보면, 그림6의 관계를 얻을 수 있다. sheet두께는 닥터 블레이드의 gap간격에 단순하게 비례해서 증가하지 않고, 부드러운 곡선을 그리면서 증가하고 있는 것을 알 수 있다. 이것은 닥터 블레이드의 gap로부터 유출되는 슬러리 양이 점성류(粘性流)와 견인류(牽引流)의 2가지 성분에 의해 구성되어 있기 때문이다.
견인류라는 것은 캐리어필름의 반송에 의해 닥터 블레이드로 부터 끌어 낸 흐름이고 점성류라는 것은 캐리어필름이 정지하고 있는 상황에서도 자중에 의해 닥터 블레이드의 gap로부터 자연적으로 흘러나오는 흐름이다. 닥터 블레이드법에 의한 sheet두께에 관해서는 식 (1)이 제안되어 있다. 그림 6중에 슬러리의 물성치 (점도, 슬러리 비중, 건조수축율)과 성형조건 (도포속도, 닥터 gap, 슬러리 액면높이)를 (1)식에 대입해서 sheet두께를 계산한 결과를 나타내었다. 계산식은 실측치에 꽤 근사한 값을 나타낸다는 것을 알 수 있다.
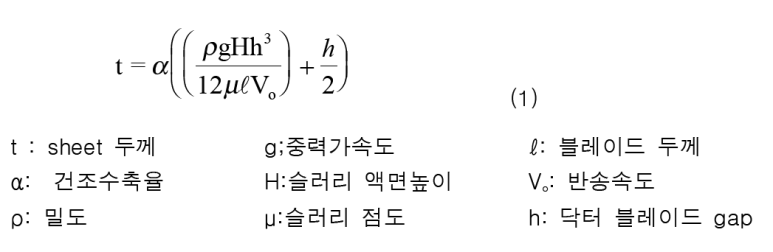
식 (1)에서, 실제에는 닥터 블레이드의 gap에 대해서 3차 함수적으로 sheet두께는 증가해 가고 있음을 알 수 있다. 이 식으로부터 도입되었듯이, sheet두께는 닥터 블레이드의 gap폭 이외에 슬러리의 점도, 건조수축률, 캐리어 필름의 반송속도, 슬러리 액멱높이에 지배되고 있다. 슬러리의 설계에 관한 요인은 건조수축, 점성유량이다, 건조수축률은 슬러리의 비휘발분양(고형분농도), 입자의 분산, sheet의 충진구조에 관계한다. 또 점성유량은 슬러리의 점도에 영향을 준다.
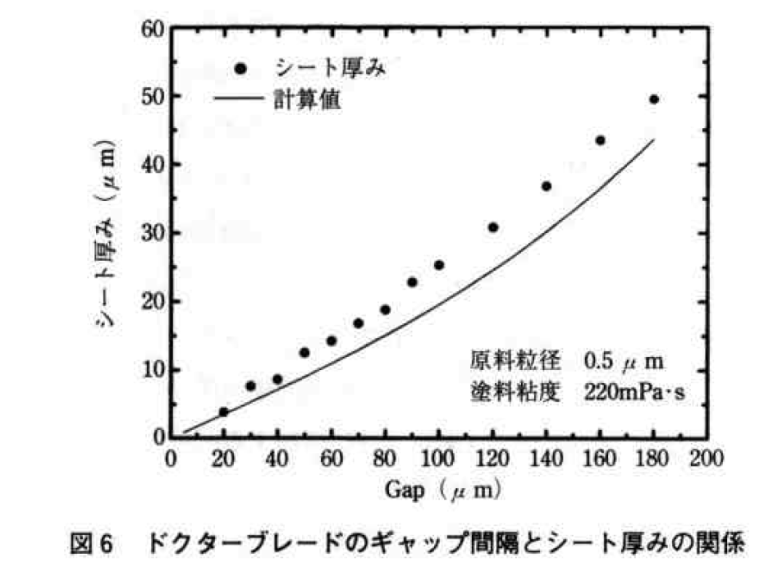
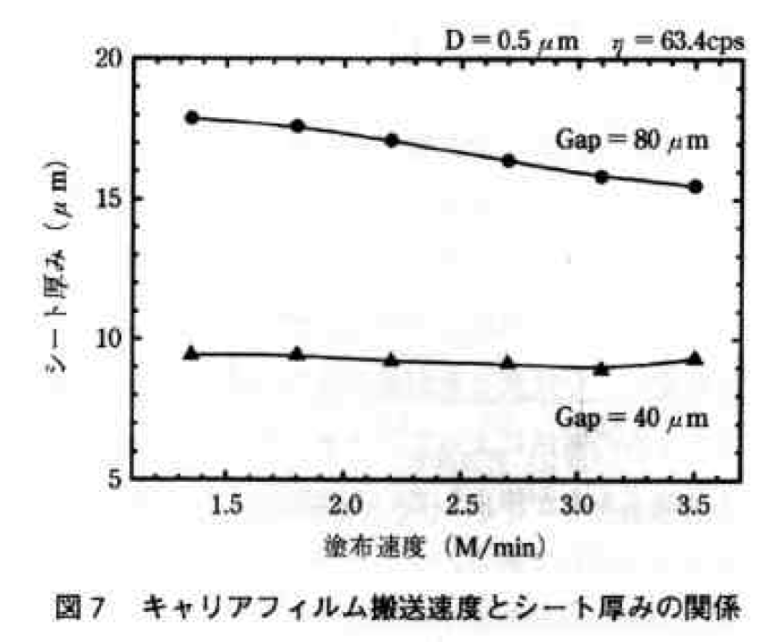
다음으로 닥터 블레이드법에 따라 성형조건이 막두께에 주는 영향을 간단히 소개한다. 캐리어필름의 반송속도에 의해 sheet두께의 변화를 그림 7에 나타내었다. 캐리어필름의 속도가 증가함에 따라서 sheet두께는 감소한다. 이것은 점성류의 영향이 작아지기 때문으로 식(1)의 관계와 일치한다. 슬러리 액면높이와 sheet두께의 관계를 그림 8에 나타내었다.
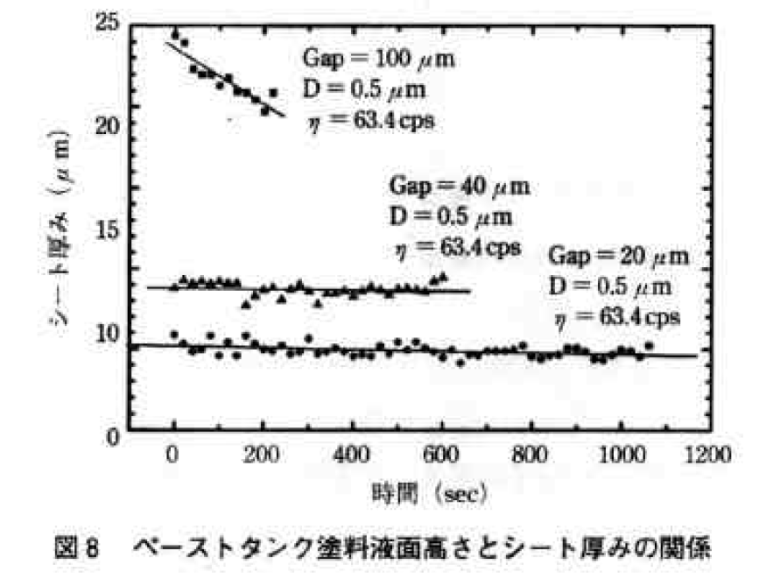
이 실험에서는 Casting head의 paste탱크에 슬러리를 한번만 보충하고, casting의 경과시간에 따라 슬러리 액면높이가 감소하는 것을 이용하였다. 이 실험 결과에서도 슬러리 액면높이가 저하함에 따라서 sheet두께는 감소함을 알 수 있다. 이들 반송속도, 슬러리 액면의 영향은 닥터 블레이드의 gap간격이 클 수록 현저하다는 것을 알 수 있다. 따라서 sheet두께의 변동을 억제하는 방법은 ①. 성형속도를 빠르게 한다. ② 액면높이를 일정하게 한다. ③ 슬러리 점도를 높게 한다. ④. 블레이드두께를 두껍게 한다 등이 효과적이다. 그렇지만 적층 세라믹 콘덴서의 sheet성형에는 sheet 두께 제어 이외에도, sheet 표면 조도, 결함발생율의 감소가 강하게 요구되어 지고 있으며, 상기조건이 반드시 우선되는 것은 아니며, 슬러리 조정조건, 건조조건에 맞추어 Casting을 해야 한다.
그림 9에 성형두께와 green sheet의 표면조도, 표면광택도의 관계를 나타내었다. green sheet의 표면조도는 성형두께가 증가함에 따라서 감소하고, 다시 증가하는 오목형의 경향을 나타낸다. 이것은 성형두께가 두꺼워 짐에 따라서 건조시간이 늦어지게 되고 leveling이 진행하기 쉽기 때문에 표면조도가 감소한다고 생각된다. 그렇지만, 더욱 막 두께를 두껍게 하면 성막한계 두께에 가까워져, orange peel 현상이 발생하기 때문에 표면조도가 나빠진다고 생각된다. 이러한, 성형조건과 성형두께에 적당한 슬러리의 설계가 중요하게 된다.
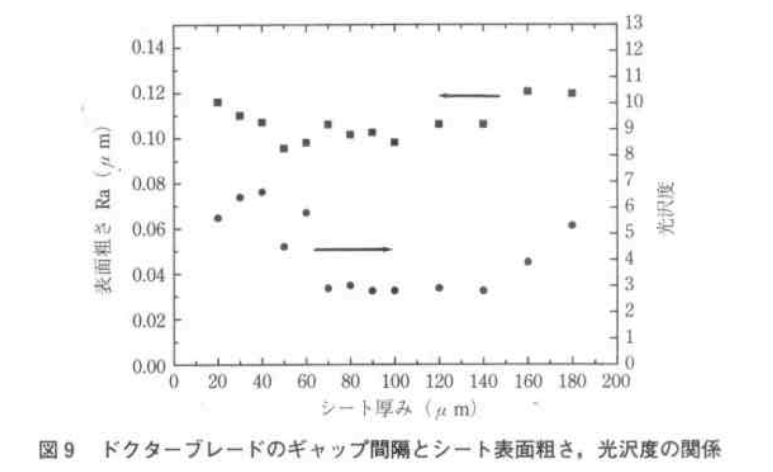
적층세라믹 콘덴서의 개발과 재료기술 및 고신뢰성화 2000
'2001-적층세라믹 콘덴서의 개발과 재료기술 및 고신뢰성화' 카테고리의 다른 글
제4장 1절 전극재료 합성기술 - 액상법 (0) | 2021.04.03 |
---|---|
제6장1절 세라믹 콘덴서의 소성기술과 구조결함제어 (0) | 2021.04.03 |
제3장 각종 합성법에 의한 유전체재료의 특징 (0) | 2021.03.30 |
제3장1절 각종 합성법에 의한 유전체 재료의 특징(고상법) (3) | 2021.03.30 |
제3장2절 각종 합성법에 의한 유전체 재료의 특징(수열법) (0) | 2021.03.30 |