2021. 3. 30. 21:45ㆍ2001-적층세라믹 콘덴서의 개발과 재료기술 및 고신뢰성화
서론
머리말
유전체재료로써 옛날부터 알려져 있는 BaTiO3을 중심으로 해서, 복합 페로브스카이트(perovskite) 유전체 재료에 관해서는 종래 고상반응법에 의한 합성법이 주류였다. 최근 적층 세라믹 콘덴서의 소형 대용량화와 더불어 한층 더 박층화와 고가의 Pd 내부전극보다 값싼 Ni 내부전극에로의 전환으로 유전체 재료의 미분말화, 고품질화와 조성의 균일화가 요구되고 있다. 이러한 요구에 부응할 만한 재료 maker를 주류로 해서 여러 가지 제법이 개발 기업화되어 왔다.
근래에 들어와서는, 이러한 신규 유전체를 사용해서 전자부품 maker의 노력에 의해 1 chip 100㎌의 적층세라믹 콘덴서가 제작 가능하게 되었다. 또한 BaTiO3는 단독으로 사용되는 것은 적고, 다수의 첨가제를 넣어서 사용하는 것이 많으므로 첨가방법에 대해서도 최근 화학적 방법에 의해 공침시키거나, 혹은 모재의 표면에 코팅하는 방법도 실용화되고 있다.
1. 유전체재료의 각종 합성방법의 소개
현재 특수한 합성방법을 제외하고 양산화되고 있는 방법을 열거하면 아래와 같다.
① 고상반응법
② 수산염법
③ 有機산염법
④ 수열합성법
⑤ Sol-gel 법
⑥ 알콕사이드법
어떤 방법도 원료로부터의 불순물의 영향을 피하기 위하여 사용 원료의 선택이 중요하다. 다음에 이러한 합성방법에 대해서 설명한다.
1.1 고상반응법
고상반응법은 일반적으로 원료로써 BaCO3와 TiO2의 고상반응에 의해 제조된다. 반응식은 BaCO3 + TiO2 = BaTiO3 + CO2이다. 원료인 BaCO3와 TiO2 중의 불순물이 전량, 제품인 BaTiO3에 혼입하기 때문에 사용원료의 선택이 중요할 뿐만 아니라 두 원료의 분산혼합을 충분히 행할 필요가 있다. 그러면 이 두 원료의 제조공법에 의한 특징과 현재 일본에서 구입 가능한 재료의 소개를 한다.
1.1.1 고상반응법에 사용되는 BaCO3의 제법과 특징
(1) 황화바륨 (BaS) 으로부터의 제조방법과 얻어진 제품의 특징
현재 거의 모든 바륨화합물은 중정석(重晶石, barite, BaSO4)으로부터 만들어 진다. 즉 BaSO4 +2C = BaS + 2CO2의 반응식으로 표시되는 것과 같이 중정석을 환원 배소하여 얻어지는 중간원료인 황화바륨(BaS)용액에 탄산가스와 반응시켜서 탄산바륨(BaCO3)을 제조한다.
(반응식 : BaS + H2O + CO2 = BaCO3 +H2S)
이 방법으로 제조된 탄산바륨의 특징: 공정이 가장 짧아서 값이 싸다는 것이다. 단점으로는 제조공정상 불순물로써 황화물이 혼재하기 때문에 내부전극인 Ni을 부식할 수 있는 가능성이 있는 것과 입도분포가 양호하지 않는 점 등이 있다.
(2) 염화바륨으로부터의 제조방법과 얻어진 제품의 특징
상기 방법에 의해 얻어진 황화바륨에 염산(HCl)을 첨가하여 염화바륨을 제조해서 중탄산 암모니움과 반응시켜서 탄산바륨을 제조한다.
(BaCl2 2H2O + NH4HCO3 + NH4OH = BaCO3 + 2NH4Cl + 3H2O)
이 방법으로 만들어진 탄산바륨의 특징: 불순물로써 황화물을 포함하지 않으므로 내부전극의 부식이 없는 점과 입도분포가 비교적 양호한 것이다. 단점으로는 불순물로써 원료의 염화바륨으로부터 염소가 존재하기 때문에 산화티탄(TiO2)과 혼합 분산할 때 응집성이 강하게 되고, 분산제의 선택이 필요하다는 것이다. 현시점에서 고상법의 BaTiO3에 이용되는 탄산바륨은 이 방법에 의한 제품이 가장 널리 사용되고 있다.
(3) 수산화 바륨으로부터의 제조방법과 얻어진 제품의 특징
수산화 바륨용액에 탄산가스와 반응시켜서 제조한다.
(Ba(OH)2 8H2O + CO2 = BaCO3 +9H2O)
이 방법으로 얻어진 제품의 특징: 미립자로 비교적 분산성이 양호한 탄산바륨을 제조 가능하다는 것이다. 수산화 바륨은 염화바륨과 수산화 나트륨으로부터 제조하기 때문에 공정이 가장 길고, 고가라는 단점이 있다.
이상 고상반응법에 사용되는 탄산바륨의 제법과 얻어진 제품의 특징을 기술하였지만, 어느 제품에 있어서도 Sr이 불순물로써 혼입하고 있기 때문에 TiO2과의 반응에 의해 SrTiO3가 생성되어 BaTiO3에 고용해서 큐리점을 저온쪽으로 이동시키므로 Sr 함유량을 충분히 주의할 필요가 있다. 현재 구입 가능한 BaTiO3용 탄산바륨의 일람 표을 그림 1에 나타내었다.
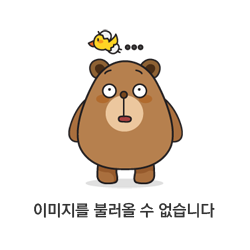
1.1.2 고상반응법에 사용되는 TiO2의 제법과 특징
TiO2제법에는 황산법과 염소법이 있다. 각 제조방법과 그 방법으로 얻어진 제품의 특징을 기술한다.
(1) 황산법에 의한 TiO2의 제조방법과 얻어진 제품의 특징
티탄철광(ilmenite, FeTiO3)에 황산과 반응시켜서 TiOSO3을 제조하고 여기에 암모니아을 넣어서 수분을 함유한 메타티탄산「TiO(OH)2」을 제조해서 이것을 열처리하여 TiO2를 제조한다.
이 제품의 특징: 고상법의 BaTiO3에 이용되는 TiO2 중 가장 저가이다. 단점으로는 불순물로써 Nb, 황산염 등을 다량으로 함유하고 있다는 것이다.
(2) 염소법에 의한 TiO2의 제조방법과 얻어진 제품의 특징
사염화티탄(TiCl4)의 염소를 산소로 치환해서 TiO2을 제조한다.
(TiCl4 + O2 = TiO2 + 2Cl2)
이 방법으로 얻어진 제품의 특징: 염화물은 비점(boiling point)이 낮아서 증류가 가능하므로 증류를 행하여 순도가 높은 사염화티탄을 사용할 수 있어서 극히 고순도의 TiO2가 얻어진다. 또한 건식에 의한 가스교환법이므로 분산성도 좋아서 미분말의 제품이 얻어진다. 그러나 고가라는 단점이 있다. 현재 고품질의 고상법 BaTiO3의 원료로써는 염소법의 TiO2가 주류를 이룬다. 제조에 있어서 어느 제법의 TiO2을 사용하더라도 통상의 제품은 안료용의 것이 많아서 알루미나, 실리카 등으로 표면처리가 되고 있지만 처리하지 않은 것도 사용할 필요가 있다. 현재 일본에서 구입 가능한 TiO2을 그림 2에 나타내었다.
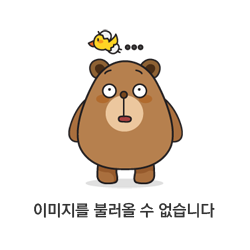
1.1.3 고상법의 제조공정
일반적인 제조공정을 그림 3에 나타내었다. 이 제법의 키 포인트(Key point)는 얼마나 TiO2와 BaCO3을 균일하게 혼합하고, 균일하게 열처리하는가 이다. 이 의미는 적절한 원료의 선택이 중요하다는 것이다. 특히 사용하는 두 원료의 분체 특성(입도, 입도분포, 비표면적)과 원료 중에 포함되어 있는 불순물에 충분히 주의할 필요가 있다.
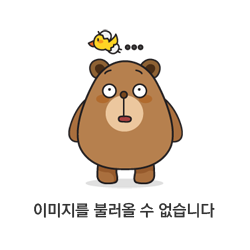
1.2. 수산염법에 의한 재료의 합성방법
수산염법에 의한 BaTiO3의 제조방법은 액상법 중에서 가장 일찍 개발 기업화된 제법이다. 원료로써 염화바륨, 사염화티탄, 수산을 사용한다. 액상법이기 때문에 최종 제품인 BaTiO3의 특성에 가장 영향을 미치는 것은 반응 조건이다.
[반응식] BaCl2 2H2O + TiCl4 + 2H2C2O4 2H2O = BaTiO(C2O4) 4H2O + 6HCl + H2O
이 반응식에 의해 얻어진 수산바륨 티타닐(BaTiO(C2O4)2 4H2O)을 열 분해해서 화학 양론적인 BaTiO3을 합성하는 것이 가능하다. 이 열 분해과정에는 여러 가지 설명이 있지만 지금까지의 연구를 종합하면 아래와 같다.
25 ~ 225 ℃; BaTiO(C2O4)2 4H2O → BaTiO(C2O4)2 + 4H2O
225 ~ 465 ℃; BaTiO(C2O4)2 → BaCO3 + TiO2 + CO + 2CO2
465 ~ 700 ℃; BaCO3 + TiO2 → BaTiO3 + CO2
이 제조법에 대해서는 고순도 BaTiO3을 합성하는 방법으로써 공업적으로 하나의 표준으로 되어 있다. 제조 공정을 그림 4에 나타내었다.

또한 합성함에 있어서 주의할 만한 점들을 아래에 표기하였다.
1) 사염화티탄 수용액을 가수분해 하지 않도록 주의할 것. 가수분해 한 원료를 사용하면, 중간품인 수산 바륨 티타놀(BaTiO(C2O4)2 4H2O)이 안 만들어 지고 최종 제품의 A/B비가 벗어나게 된다.
2) 탈수산의 온도가 최종 제품의 입도에 영향을 미치기 때문에 치밀한 관리가 필요하다.
3) 염산을 완전분리 하지 않으면 최종 제품의 전기특성을 열화시킨다.
4) 1몰의 제품을 합성하면 6몰의 염산이 발생하므로 배수관리에 충분히 주의할 것.
수산염법에서는 고상법에 비해 원료인 사염화티탄, 염화바륨, 수산 모두 고순도품의 구입이 간단하다. 또한 액상법이기 때문에 원료의 분체특성은 최종 제품의 특성에는 관계하지 않는다. 그러나, 최종 제품인 BaTiO3의 Ba/Ti 비를 반응 조건에서 제어할 필요가 있다. 또한 생성한 수산 바륨 티타놀로부터 부착하는 염산을 물에서 세척시 수산 바륨 티타놀로부터 Ba이 용출해서 최종 제품인 BaTiO3의 Ba/Ti 비가 1이하, 즉 Ti-rich로 되기 때문에 충분히 주의할 필요가 있다.
수산바륨티타놀의 입도는 반응온도와 반응시간에 의해 결정되지만 응집체로 얻어지기 때문에 하소 후에 이 응집체의 골격이 남고, 최종 제품인 BaTiO3의 조대 응집 입자를 생성하기 쉬운 것이 문제이다. 따라서 적당한 하소 조건의 선정과 조대 입자의 해쇄가 필요하다. 종래부터 수산염법의 각종 개량 방법이 제안되어 오고 있다. 그 중에서 사염화티탄 수용액이 가수분해를 받기 쉬워서 조성제어가 어려운 것에 주목해서 수산과 Ti(OC4H9)의 이소프로파놀 용액을 준비해서 이 혼합용액에 초산바륨 수용액을 반응시켜서 수산바륨티타놀을 얻는 것이 제안되고 있다. 이 방법에서는 수산이소프로파놀 용액과 Ti(OC4H9)이소프로파놀 용액에 의해서 생기는 H2TiO(C2O4)2가 초산바륨과 반응해서 수산바륨티타놀(BaTiO(C2O4)2 4H2O)이 생성되는 것으로 사료된다. 반응식을 아래에 나타내었다.
H2TiO(C2O4)2 + Ba(CH3COO)2 + 4H2O BaTiO(C2O4)2 4H2O + 3CH3COOH
현재 구입 가능한 수산염법에 의해 얻어진 각종 BaTiO3의 data을 그림 5에 표시하였다.

1.3 유기산염법에 의한 BaTiO3의 합성방법
이 방법은 수산염법에 의한 제법과 같이 오래 전부터 연구되어 온 것이다. 그러나 가격적으로 수산염법에 비해서 고가라서 기업화되지 않았다. 제법을 간단히 설명한다. 유기산바륨 수용액과 유기산티탄 수용액을 반응시켜서 제조된 BaTi(C6H6O7)3 6H2O을 열 분해해서 BaTiO3을 얻는다. 분해과정을 다음에 나타내었다.
20 ~ 210 ℃; BaTi(C6H6O7)3 6H2O → BaTi(C6H6O7)3 + 6H2O
210 ~ 250 ℃; BaTi(C6H6O7) → BaTi(C5H4O4)3+ 3CO2
250 ~ 360 ℃; BaTi(C5H4O4)3 → TiO2.Ba(C5H4O4) + 2C5H4O3
360 ~ 600 ℃; TiO2 Ba(C5H4O4) → BaTiO3 + X
이 제조방법에 대해서는 공업적인 의미보다 분해과정의 연구 등 학술적인 대상으로 되어 왔다. 이 방법의 특징은 유기산바륨 수용액과 유기산티탄 수용액의 반응에 있어서 수용액의 pH을 3.2 이상으로 하면 제조되는 BaTiO3의 Ba/Ti 비가 2의 제품이 되고, pH을 최적의 조건으로 하면 A/B 비가 1로 된다는 점이다.
1.4 수열법에 의한 BaTiO3의 합성법
종래부터 수산화바륨과 메타티탄산TiO(OH)2의 물을 함유한 염을 상압하에서 가열해도 BaTiO3을 제조 가능한 것이 알려져 있으나 이것을 100℃, 1기압이상의 고온 고압하에서 처리하면 상압에서 보다 결정성이 좋은 BaTiO3가 생성된다. 이것이 수열법에 의한 제조 방법이다. 반응식은 Ba(OH)2 + TiO(OH)2 → BaTiO3 + 2H2O로 나타내어 진다. 공업적으로는 수산화 바륨 대신에 염화바륨으로 출발해서 알칼리를 첨가하여 수산화바륨으로 해서 공업적 반응조건에 대해서는 문헌, 특허 등에서는 200℃, 5시간이 예시되어 있다. 수열합성법에 의한 BaTiO3 제조에 관한 문제점 및 주의사항을 아래에 나타내었다.
1) 원료인 수산화바륨에는 그 제조상, 불순물로써 Na 성분이 포함되기 때문에 사용 전에 Na 성분을 가능한 제거할 필요가 있다. 그렇게 하지 않으면 최종 제품의 전기특성에 악영향을 미치게 된다.
2) 제조된 BaTiO3는 미분말이기 때문에 어느 정도의 하소를 행하고 입도의 증대를 꾀할 필요가 있다. 하소 및 소결 시에 입자 중에 일부 존재하고 있던 (OH)기가 빠져 공공이 생성한다(그림 6). 이 점이 수열합성법의 단점이다.
3) 합성반응 후의 물세척 과정에서 Ba이 소실되어 BaTiO3의 Ba/Ti 비가 벗어날 가능성이 있기 때문에 어떻게 하면 1로 유지할 것인가에 대한 연구가 필요하다.
4) Perovskite 구조의 B site의 Ti을 일부 Zr로 치환한 제품도 제조 가능하다.
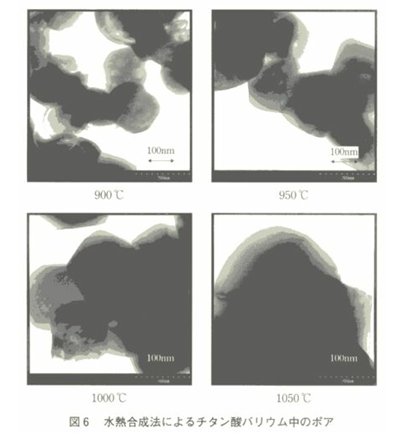
1.5 Sol-Gel 법에 의한 합성 방법과 제품의 특징
바륨의 수산화물의 겔(Gel)과 티탄의 졸(Sol)을 혼합해서 건조(Spray dryer)하고 하소, 분쇄해서 제품으로 만드는 방법이다. 이 방법의 중요한 점은 공정 도중에 조성분석을 어느 정도 정밀하게 행하는가 이다. 무기 혹은 유기의 염의 졸 또는 겔 혼합하는 방법이기 때문에 여러 가지 복합재료가 제조 가능하고 특히 적층세라믹콘덴서 중에서 F특성용의 각종 첨가제를 최초로부터 완전 고용시켜서 사용하는 계의 재료에는 최적이며 B특성의 Core-Shell 구조를 갖는 재료에는 맞지 않다. 또한 최근에는 Perovskite 구조의 ABO3 내의 B site의 티탄은 미분말의 산화티탄을 이용해서 A site만을 각종 금속염의 졸을 사용하는 것 등, 종래의 고상법과 졸-겔법의 중간적인 방법도 채용되기에 이르렀다. 이것은 종래와 달리 현시점에서는 각종 원소의 초미분말이 공업적 규모로 구입 가능하기 때문이다. 이 방법에서의 주의 사항은 졸 없이 겔의 혼합 시의 분산과 건조 작업이며 특히 광범위하게 건조하면 팬케익과 같이 되고 말고, 후 공정에서 문제를 발생하므로 대부분의 경우는 유기용제를 포함한 슬러리을 스프레이 드라이어을 이용해서 건조시켜서 후 공정의 하소공정으로 옮겨가는 것이 훨씬 좋다. 이 방법으로 제조된 복합 페로브스카이트 구조의 사례를 그림 7에 나타내었다.
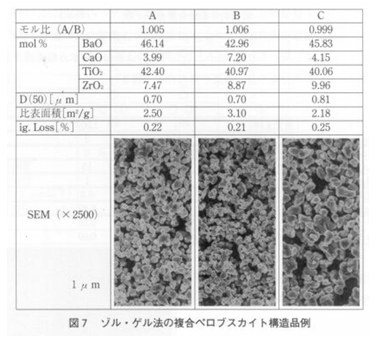
1.6 알콕시드법에 의한 합성법과 얻어진 제품의 특징
알콕시드법에 의한 제조 방법은 Dupont 社 등에 의해 20년쯤 전에 연구되어 오다가 원료계가 고가이기 때문에 실용으로는 제공되지 않았다. 그러나 유전체 메모리의 실용화 등, 적층 칩 콘덴서의 소형, 고용량화에 의한 고부가가치화에 따른 고가의 재료도 사용할 수 있는 상황이 되어 왔다. 이미 이 방법에 의해 얻어진 제품으로부터 전자부품의 제작이 시도되어 지고 있다.

Dupont 社의 제조방법을 소개하면, 그림 8에 나타낸 공정도와 같이 티탄의 알콕시드로써 isoproxide가 아닌 butoxide(Ti(O-Bu-n)4)를 이용해서 두 성분을 제트 혼합기을 이용해서 급속히 혼합한 후 이 혼합물을 돌리면서 가열하여 생성시킨 침전을 결정화해서 제품을 얻는다.
이때 BaTiO3의 Ba/Ti 비를 1로 하기 위해서 원료인 수산화바륨을 Ti에 대해서 약 10 mole% 과잉으로 첨가할 필요가 있다. 이 방법이외에 Ba과 Ti 모두 알콕시드을 이용한다. 완전 알콕시드법에 의한 제조법도 잘 알려진 방법이다. 특히 최근 고용량메모리로서 개발이 급속히 진행되고 있는 유전체 메모리의 제법으로는 완전 알콕시드법에 의해 각종 유전체조성의 알콕시드 용액을 만들고 기판 위에 도포해서 가수 분해시켜서 유전체 막을 제조할 때 많이 사용되어 지고 있다. 입자로 만들 때에는 적당한 가수 분해 조건을 설정하면 미립자이면서 구상의 아주 입도분포가 좋은 제품이 얻어진다(그림 9).
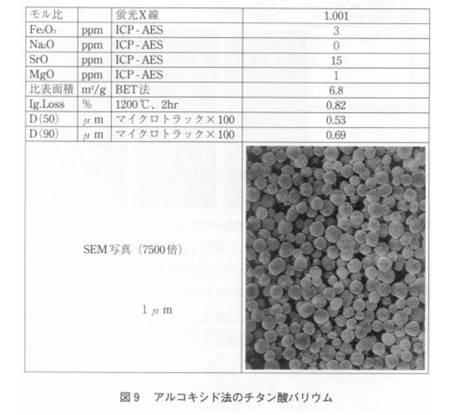
2. 각종 합성법에 의한 유전체재료의 비교
세라믹콘덴서의 원료인 BaTiO3을 중심으로 각종 합성방법과 얻어진 제품에 대해서 서술하였는데 각 방법에 의해 제조된 제품의 특징의 비교표를 표 1에 나타내었다. (注: 유기산염법은 수산법으로 얻어진 제품의 특징과 거의 동일하므로 생략) BaTiO3 만의 합성은 거의 위에서 서술한 바와 같으나, 최근은 완전한 배합제 첨가의 재료에 관해서는, 上記이외 또는 상기 방법의 혼용법도 채용되고 있다.
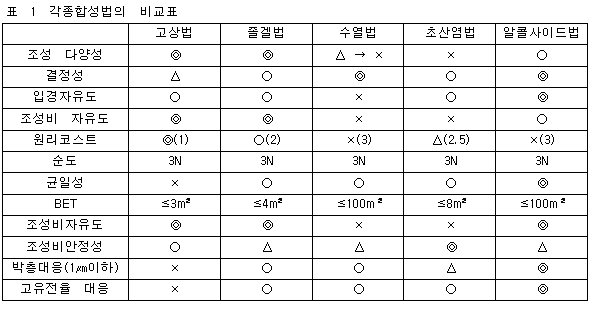
맺음말
최근 IT 관련 산업의 촉진과 더불어 전기회로에 없어서는 안될 콘덴서의 수요가 확대되고 있다. 콘덴서 중에서도 특히 적층세라믹콘덴서는 그 주파수 특성의 양호함 및 표면 실장의 편리함에 의해 전년도 대비 40%을 넘는 급성장했다. 세라믹콘덴서의 분야는 세계에서 일본이 기술적으로도 생산 수량적으로도 앞서 있다. 지금은 자칫하면 각 분야에서 歐美에 압도되어 있는 상황에서 일본이 자랑할 것이 거의 없는 기술이라 말할 수 있다. 원료 maker 및 전자부품 maker가 서로 협력해서 다시 한번 발전하기를 기대한다.
적층세라믹 콘덴서의 개발과 재료기술 및 고신뢰성화-기술정보협회 2000 (제3장)
'2001-적층세라믹 콘덴서의 개발과 재료기술 및 고신뢰성화' 카테고리의 다른 글
제4장 1절 전극재료 합성기술 - 액상법 (0) | 2021.04.03 |
---|---|
제6장1절 세라믹 콘덴서의 소성기술과 구조결함제어 (0) | 2021.04.03 |
제5장 2절 적층 성형 기술 (0) | 2021.04.03 |
제3장1절 각종 합성법에 의한 유전체 재료의 특징(고상법) (3) | 2021.03.30 |
제3장2절 각종 합성법에 의한 유전체 재료의 특징(수열법) (0) | 2021.03.30 |