2022. 5. 21. 20:24ㆍ2020-적층세라믹콘덴서의 재료-제조-실장기술과 최신기술
1. 단자 전극 재료
단자전극의 역할은 MLCC의 내부전극과 전자회로를 접속하는 것이다. 그러므로 MLCC와도 충분한 접착강도를 가짐과 동시에 회로기판과 납땜으로 전기적으로나 기계적으로 충분한 강도로 접속되어야 한다. 단자 전극부의 구조의 모식도를 그림 1에 나타내었다. 단자 전극 재료로는 Ni 혹은 Cu가 이용되고 있지만, Cu가 보다 일반적이다. Cu 단자 전극 페이스트를 MLCC 단면에 도포, 건조 후에 소부라고 하는 열처리를 행하여 단자 전극이 형성된다. MLCC의 Ni 내부 전극과는 금속끼리여서 소부 시 확산 반응에 의해 충분한 접속이 가능하다. 그렇지만, MLCC의 세라믹 유전체와는 「산화물과 금속」이라고 하는 큰 성질이 다른 물질의 조합이므로, 소부한 것만으로는 충분한 접착 강도를 얻을 수 없다. 이에 단자 전극 중에는 「산화물과 금속」을 접착시키기 위한 풀 역할을 하는 Glass Frit가 더해져 있다. 또한 단자 전극 표면에는 Ni와 Sn의 2층이 전기도금되어 있다.
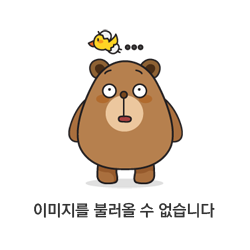
회로기판에 솔더링할 때 솔더에 의해 단자전극이 침식된다. 이른바 솔더침식을 방지하기 위해 Ni도금이, 솔더에 대한 젖음성을 높이기 위해 Sn도금이 되어 있다. 도금욕으로는 Ni도금에서는 와트욕이나 설파민욕이, Sn도금에서는 황산욕이나 글루콘산 등의 유기산욕이 이용된다. Sn도금 막에는 솔더의 산포가 있으면 Tombstone 현상 또는 맨해턴 현상으로 불리는 칩 섬 등 납땜 불량이 일어날 수 있기 때문에, 기판에 탑재의 위치 정밀도와 도금 표면의 성능은 중요하다.
맨해튼 현상은 소형 칩에서 두드러지게 되기 쉬우니 단자 전극 이외에 회로 기판의 랜드 패턴의 형상 설계 및 땜납량에 배려가 필요하다. 또한 도금에 있어서 단자 전극이 포러스하면 포아 내에 도금 성분이 남아서 납땜시 파열하고 "Spattering"이라고 불리는 현상이 일어난다. 이로 땜납이 기판상을 오염시킬 수가 있다, 그래서 단자 전극은 치밀한 것이 요구되므로 단자 전극 표면의 연속성을 높이기 위해서 구형의 Cu입자와 후 Flake상의 Cu입자를 혼합한 단자 전극 Paste를 이용하는 것이 일반적이다.
Ni단자전극의 경우에는 Ni입자와 유전체재료의 혼합물 페이스트가 도포, 건조한 후에 소결되어 형성된다. Pd-MLCC의 경우에는 Ag단자전극이 이용되므로 소부는 대기중에서 행할 수 있으나 Ni-MLCC의 경우에는 Cu단자전극이므로 비산화성 분위기에서 소부하여야 한다. 따라서 Glass frit에는 내환원성이 필요하며 인규산연계의 Glass frit을 사용할 수 없으며 Sr계나 Ba계의 유리플릿 또는 결정화 Zn계의 Glass frit 등이 이용되고 있다.
도금막을 포함한 단자 전극은 회로 기판과의 접속 신뢰성이라는 점에서 매우 중요하다. 단자 전극에 관련된 신뢰성상의 주요 과제로 다음과 같은 항목을 들 수 있다.
1) 납땜 시 Thermal서멀클랙
2) 기판의 휨에 의한 크랙
3) 히트 사이클에 의한 땜납의 취화 크랙
이다. 이들 과제를 클리어하는데 있어서 단자전극의 역할은 매우 크다. 또한 실장밀도의 고밀도화에 수반하는 MLCC의 소형화에 의해 단자전극 두께의 박층화와 단자전극 형상의 고정밀도화가 진행되고 있어 단자전극의 중요성이 더해지고 있다.
2. Thermal Crack
MLCC를 회로기판에 납땜하는 방법으로서 최근에는 예열식 리플로우로가 이용되고 있다.예전 플로우 방식의 웨이브 땜납보다는 열충격이 작지만 그래도 납땜에 따른 열충격이 MLCC에 가해져 드물게 Thermal 크랙이라 불리는 크랙이 발생할 수 있다. 대표 예를 그림 2와 같다. 대부분의 경우 단자 전극하에서 크랙이 발생한다.
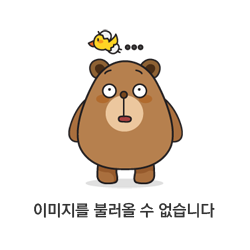
단자전극을 소부시키기 전의 MLCC 소지에서는 Thermal크랙이 발생하지 않는다. 즉, 단자전극과 MLCC의 반응이 원인이며, 단자전극과 내부전극의 상호확산반응 및 Glass frit과 유전체의 반응 양쪽의 균형을 이룰 필요가 있다. Thermal 크랙의 경우 크랙을 발생시키는 구동력과 그에 견디는 저항력의 차이로 발생 여부가 결정된다. Thermal크랙 발생 구동력은 열충격, 즉 온도와 승온속도이다. 단자 전극은 Ag나 Cu 등의 금속이 주성분이며 유전체 세라믹스보다 열전도율이 매우 높고, 또한 땜납과의 계면에서의 열전달도 매우 좋다. 따라서 용융땜납에 접했을 때 단자전극은 바로 200~230℃에 이르지만 유전체 세라믹스 쪽은 아직 실온에서 예열온도이다.더욱이 단자전극은 내부전극과 상호확산으로 합금을 형성하고 있으며 내부전극도 빠르게 승온하여 팽창한다. 따라서, 이 온도차가 Thermal 크랙의 원인으로 생각된다.
그렇지만 실온에서 200~230℃까지의 승온속도가 유전체 세라믹스와 단자전극에서 동일하더라도 실온에서 200~230℃까지의 온도차에 따른 선팽창률 차이만큼 응력이 발생한다.이것은 승온 속도에서는 해소하지 않고, 이것도 Thermal 크랙의 요인이다. 한편 Thermal 크랙 발생에 대한 저항력은 유전체 세라믹스의 강도이다. MLCC 내에 delamination이나 크랙이 있는 경우에는 당연하지만 Thermal 크랙은 발생하기 쉽다. 따라서 세라믹스 중에 delamination이나 크랙 등의 구조결함이 없는 것은 필수적인 조건이다. 또한 기계적 강도를 높이기 위해 소결 밀도를 높이는 것이나 grain크기를 키우지 않는 것은 최소한 필요하다.
미시적인 시점에서 Thermal 클럭을 보면 단자전극과 내부전극의 접점 부근 구조와 화학조성이 매우 중요하다.MLCC의 단자전극 부분 미세구조의 대표적인 예를 그림 3에 나타내었다. 단자전극 금속성분은 Pd-MLCC의 경우에는 Ag 또는 Ag/pd, Ni-MLCC의 경우에는 Cu 또는 Ni이다. 유리성분은 유전체와 반응할 뿐만 아니라 조성에 따라 단자전극 금속(Ag나 Cu)의 소결을 촉진하는 경우도 있어 단자전극과 내부전극 혹은 세라믹스의 계면구조에 큰 영향을 미친다. 이 계면에서의 반응과 구조는 Thermal 크랙의 가장 큰 요인이 된다.
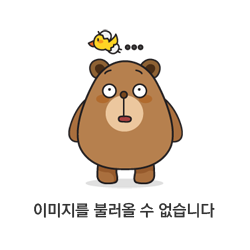
내부 전극과 단자 전극의 금속 성분은 각각 Pd 및 Ni이고, 단자 전극의 그것은 Ag와 Cu이다. Pd-Ag계 및 Ni-Cu계는 각각 전율 고용계이다. 따라서, 단자전극 소부시 내부전극-단자전극 계면에서는 확산반응에 의해 합금이 형성된다. 모든 계에서 내부전극금속이 단자전극금속보다 융점이 높으므로 예상되듯이 단자전극 성분이 내부전극쪽으로 확산되기 쉽다. 즉 내부전극의 Pd나 Ni가 단자전극의 Ag나 Cu중에 확산하는 속도보다 Ag나 Cu가 Pd나 Ni중에 확산하는 속도가 더 크다. 그 결과 계면근방의 내부전극 부피는 증가하고 세라믹스에 강한 응력을 준다. 이때 내부전극을 끼고 있는 유전체 세라믹스가 단단한 상태라면 내부전극은 부피 증가만큼 단자전극 쪽으로 내밀게 된다. 유전체 세라믹스와 단자 전극의 접착력을 상회하는 힘이면 유전체와 단자 전극 사이에 큰 공극이 생겨 그림 4와 같다.
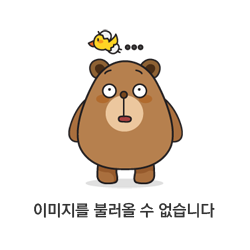
만약 내부전극을 끼고 있는 유전체 세라믹스가 글래스 플릿의 확산에 의해 연해져 있다면 내부전극은 세라믹스 쪽으로도 팽창할 수 있고, 그만큼 세라믹스는 소성적 변형을 일으킨다. 내부 전극의 부피 팽창이 세라믹스의 소성적 변형을 넘는 속도로 진행되면 세라믹스는 내부 전극 계면에서 마이크로 크랙을 발생하여 그림 3과 같이 된다. 마이크로크랙에 의해 내부전극팽창의 응력을 충분히 흡수할 수 있으면 좋으나, 충분히 흡수할 수 없는 경우에는 세라믹스 측에 상당히 강한 잔류응력이 남아 버린다. 이 강한 잔류응력을 완화할 수 있는지 없는지는 glass frit의 확산된 세라믹스의 성질에 달려 있고, glass frit의 조성과 세라믹스에 대한 반응성이 열쇠가 된다. 납땜시의 열충격으로 단자전극이나 내부전극이 열팽창할 때에 이 마이크로크랙이나 강한 잔류응력 때문에 Thermal 크랙이 발생하는 것이다.
3. 기판 휨크랙
MLCC의 탑재된 회로기판이 전자기기에 조립, 장착될 때 기판에 다양한 응력이 가해질 수 있다.회로기판에 휨응력이 가해진 경우에는 땜납으로 고정된 MLCC에 대해서도 상당한 힘이 가해져 크랙을 발생시키기도 한다.그래서 MLCC와 같은 표면실장 부품에는 휨 강도라는 특성이 중요해진다.휨크랙 측정방법을 그림5와 같다.
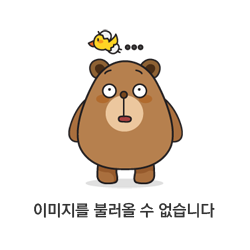
단자전극을 형성한 MLCC를 땜납경을 일정하게 제어한 glass 에폭시 기판에 리플로우로 납땜하는 것이 일반적이다. 이 기판의 뒷면을 1mm/s의 속도로 가압하고, JIS-C6429에 따라 MLCC의 정전용량이 12.5% 저하되었을 때의 기판의 변위량이 휨량으로 정의된다. 이때의 응력이 휨강도라 불린다. 휨시험에 의해 MLCC에 크랙이 들어가 내부의 콘덴서층의 일부가 단자전극과의 접속을 잃기 때문에 정전용량이 저하된다. 실제 휨크랙의 예를 그림6에 나타내었다.
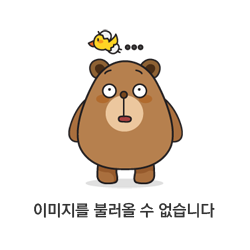
통상 단자전극 근방에 크랙이 들어가 내부의 유효전극층에 크랙이 걸리는 경우도 많다. 이러한 경우 MLCC에 전계가 걸리면 크랙을 통해 대향전극간이 쇼트에 이르러 중대한 사고를 일으킨다. 따라서, 휨크랙은 MLCC 사용자들이 가장 싫어하는 현상 중 하나이다.
휨 크랙의 경우에도 thermal 크랙과 마찬가지로 크랙을 발생시키는 구동력과 그에 견디는 저항력의 겸비로 발생 여부가 결정된다. 구동력은 기판의 휨에 의한 응력이며 저항력은 MLCC의 기계적 강도뿐만 아니라 구동력을 완화하는 인자도 포함된다. 휨 강도의 주된 인자는 구조 인자와 재료 인자의 두 가지로 크게 나눌 수 있다. 구조 인자로는 기판의 두께, 땜납의 양, 땜납의 젖음량, 단자 전극의 치수, 실장 상태(랜드로부터의 어긋남) 등을 들 수 있다. 재료 인자로는 유전체 세라믹스의 강도, 내부 전극과 단자 전극의 반응, 유리 프릿과 유전체의 반응 등을 들 수 있다. 재료인자로서 단자전극 중 glass frit의 조성과 양과 소부조건은 thermal 크럭 때와 마찬가지로 매우 중요한 것으로 보고되고 있다.
휨시험 시 응력분포를 유한요소법으로 해석한 예가 보고되었다.이를 그림7에 나타내었다. 휨의 응력이 랜드 근처의 MLCC의 소지에 집중되어 있음을 알 수 있다. 따라서 휨크랙은 이 응력집중부를 기점으로 하여 발생한다. 이때 MLCC의 단자전극의 단부를 모식적으로 그림 8에 나타내었다. 단자 전극 중에는 유전체 세라믹스와의 접착을 위해 glass frit이 포함되어 있다. 단자 전극 소부로 단자 전극부에는 큰 잔류 응력이 남는다.
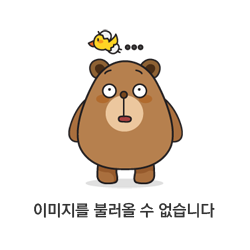
여기서 기판의 휨에 의한 응력이 중첩되어 파괴에 이르는 것이다. 기판의 휨에 의한 기계적 외력이 가해질 때 단자전극중의 유리가 확산된 부분과 확산되지 않은 부분의 계면 부근에서 크랙이 발생하기 쉬운 것으로 알려져 있다. 유리가 확산된 부분과 그렇지 않은 부분의 기계적 성질이 다르기 때문에, 그 계면이 크랙의 기점이 되기 쉽다. 유전체 세라믹스의 경우에도 압축응력에는 비교적 강하고 인장 응력에는 약하다는 세라믹스 공통의 성질이 있다. 따라서 표면에 압축응력을 남겨두면 강도는 강해진다. 단자 전극 중의 glass frit 성분을 MLCC 표면 전체에 확산 처리했을 경우에는 휨 강도도 강해지지만, 단자 전극 표면에 유리층이 남기 쉽고 대폭적인 비용 상승 요인이 되기 때문에 현실적이지 않고 실현되지 않았다. 휨크랙에 대한 대책으로는 상술한 바와 같은 재료인자를 고려하여 glass frit 의 조성과 양의 적정화 및 소부조건의 최적화가 이루어지고 있다.
4. 납크랙
MLCC의 신뢰성을 고려할 때 구현의 신뢰성도 매우 중요하다.유 전 특성이나 절연 저항에 대해서는 온도 안정성, 경시 안정성, 환경 안정성 등에 눈이 가기 쉽지만 실장의 신뢰성도 충분히 고려해야 한다. 기판에 납땜된 후의 실사용에 있어서 기판에서 떨어지면 기능을 할 수 없게 되어 버릴 뿐만 아니라 경우에 따라서는 중대한 사고로 이어질 수 있다. 실장의 신뢰성 항목으로는 일반적으로 실장 후에 열사이클 시험이 이루어진다. -55~125℃의 히트 사이클이 1,000~3,000 사이클 정도 이루어진다. 통상적인 Ni-MLCC에 대해 열사이클 시험을 실시했을 때의 단자전극 및 납땜 부분의 변화를 그림9에 나타내었다.
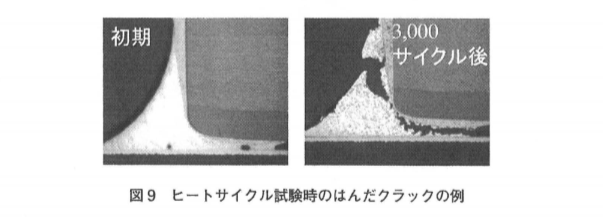
2,000사이클의 열사이클 시험에서 이미 납땜에 크랙이 들어가 3,000사이클에서는 전기적 접속이 더 이상 유지되지 않는 상황에 이르렀음을 알 수 있다. 유한요소법(FEM)에 의한 해석에서도 드러나는 바와 같이 열사이클의 열충격에 의해 땜납 접합부분에 강한 응력(인장과 압축의 반복)이 반복적으로 가해지는 것을 알 수 있다. 이것에 의해 땜납이 취화되어 크랙이 발생한다. 땜납이 약해져 버리기 때문에 최종적으로는 회로 기판에서 MLCC가 빠져 버릴 위험성이 있다. 이 문제를 해결하기 위해 기판의 물성, 땜납 조성, 땜납량, 랜드의 형상 등의 검토도 중요하지만 MLCC에도 단자 전극으로서의 대책이 필요하다.
'2020-적층세라믹콘덴서의 재료-제조-실장기술과 최신기술' 카테고리의 다른 글
제3장1절 티탄산바륨의 유전분극기구 (0) | 2022.05.22 |
---|---|
제2장 5절 특수한 단자전극 (0) | 2022.05.22 |
제2장3절 내부전극용NI분말의 제조법(2항 분무열분해법, PVD법) (0) | 2022.05.21 |
제2장3절 내부전극용 Ni분말의 제조법(1항CVD법) (0) | 2022.05.16 |
제2장2절-3 티탄산바륨의 합성법(2) - 수열합성 (0) | 2022.05.15 |