2022. 4. 30. 16:31ㆍ2020-적층세라믹콘덴서의 재료-제조-실장기술과 최신기술
1장 MLCC의 개요
1절 적층 세라믹 콘덴서의 역사
[적층 세라믹 콘덴서의 역사]
적층 세라믹 콘덴서 (Multi-Layered Ceramic Capacitor : MLCC) 는 해마다 생산증가의 일로를 걷고 있다. 1990년에 전 세계에서 약 1,000억 개의 생산량이었으나 2016년에는 전 세계에서 약 3조 개나 생산된 것으로 추측되고 있다. 최근에는 스마트폰 이외에도 IoT 혹은 자동차의 EV화나 자동운전 기술 등에 의해 수요가 급속히 확대되고 있다. Connected (커넥티드, 연결), Autonomous (자동운전), Shared & Service(셰어링과 서비스), Electric (전기자동차)의 이른바 CASE라 불리는 키워드가 자동차의 방향성을 나타내는 지침이라 불리고 있다.
1960년대에 얼터네이터, 이그나이터, 스타터라고 하는 전장품에 반도체 소자가 채용된 이후, 카 엘렉트로닉스화의 걸음이 착실하고 급속히 진전해 왔다. 최근에는 선진 운전 지원 시스템(ADAS)으로서 다양한 기능이 개발되고 있다. 모든 기능에 전자제어, 전동화가 적용되어 전자제어유닛(ECU)의 수는 차당 약 70개에 달하며, 고급차에서는 100개 이상의 ECU를 사용하고 있다고 한다. 반도체 소자가 그만큼 많이 사용되면 수동 소자의 콘덴서도 노이즈 대책, 전압 강하 대책 혹은 전원 전압의 평활화 등에 많이 필요하며, 그 중에서도 MLCC는 높은 신뢰성, 사용하기 편리함, 혹은 소형 저가격 등의 이유로 차량 탑재 전자회로에 많이 사용되고 있다.
향후, 통신 기술의 5G에 의해서 폭발적 증가도 예측되고 있다. 부품의 실장기술이 리드스루 실장에서 표면실장기술로 변혁함으로써 각종 전자기기의 경박단소화가 가능해지고, 이에 따라 단판형 원판 콘덴서에서 적층형 MLCC로 대체됨으로써 일거에 콘덴서의 소형화가 진행되어 왔다. 이로 인해 전자기기는 한층 더 소형화가 진행되어 오늘날의 휴대형 전자기기로 진화해 온 것이다. 세라믹 콘덴서가 탄생한 이후 세라믹 콘덴서 혹은 MLCC에 항상 요구되어 온 것은 다음 4개 항목이다. 1)소형화, 2)고용량화, 3)고신뢰성화, 4)저가격화이다. 이들 4개의 시장 요구는 향후도 변함없는 것이라고 생각되고 있다.
세라믹 콘덴서 혹은 MLCC의 역사는 의외로 오래 전부터 시작되었다. MLCC의 역사는 한마디로 저가화의 역사라고 할 수 있다. MLCC의 역사를 모식적으로 그림 1에 나타낸다. 디스크 타입의 콘덴서가 처음 발표된 것은 1920년, Siemens사로 부터였다. Ti02 세라믹스를 유전체, Ag를 전극으로 하는 것이었다. 이후 1933년 MLCC 원형이 발명되어 US Naval Research를 중심으로 개발이 진행되었다.
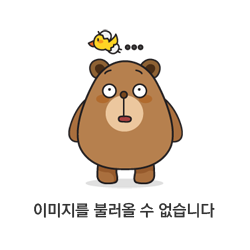
1943년 DuPont사로부터 적층형 콘덴서가, Ti02 세라믹스와 Ag 전극의 조합으로 발표되었다. 1942년 미국에서 Wainer와 Salomon이, 1944년 일본에서 오가와와 와큐가, 마찬가지로 1944년 소련에서 Vul과 Goldman이 BaTi03을 각각 독립적으로 발견하였다. 그 경이적인 유전율을 높히기 위해서 많이 연구되기 시작했다. 이후 1947년에 Howatt가 오늘날 MLCC의 기초가 되는 시트 성형기술을 개발하여 Ti02 based 유전체와 AuPt 전극을 사용하여 MLCC의 원형이라고 할 수 있는 것을 제작하였다. 드라이 시트 양면에 AuPt 전극을 코트하여 여러 층을 쌓아 올린 후 소성하여 일체화된 블록을 얻는 데 성공했다. 이 방법에 의해 작은 부피로 큰 정전용량을 얻었다. 이 일체소성은 고온소성이 필요하기 때문에 값비싼 귀금속 페이스트를 필요로 했다. 그래서 그들은 시트를 소성 후에 Ag 페이스트를 인쇄하고, 거기에 리드선을 소량의 솔더로 납땜, 혹은 스폿 용접으로 장착하여 쌓음으로써 큰 정전용량을 얻었다. 그것을 Sprague사가 제조한 것을 그림2에 나타내었다. 한편, 그들의 시트 성형기술은 그 후의 원판콘덴서의 고생산성 제조시스템의 시트 성형, 타발공법의 기초가 되는 것으로 획기적이었다. 산업적으로는 1980년대까지 시트 성형 타설 공법에 의한 원판 콘덴서가 전성기를 이루었다.
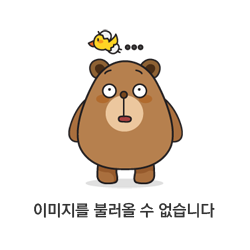
Howatt의 시트 성형기술 발표 이후, 미국 RCA사와 미국 해군연구소가 중심이 되어 BaTiO3기 유전체와 Pt전극을 이용한 MLCC의 개발이 진행되었다. 그러나 고가의 Pt를 사용하였기 때문에 MLCC는 군용으로 공급되어 민간용으로는 좀처럼 보급되지 않았다. 그러다가 1960년대에는 Pt보다 당시는 압도적으로 저렴한 Pd (당시는 Pt가 약 2,000엔/g, Pd가 약 450엔/g)을 내부 전극으로 이용한 MLCC가 미국에서 개발되었고, 일본 기업도 1970년대에 그 기술을 도입하였다.
그러나 Pd도 귀금속으로 고가였기 때문에 이들 MLCC 보급에는 전극의 비용이 큰 벽이 되었다. 그런 상황에서 1963년에는 Herbert가 비금속 전극(Base Metal Electrode : BME)을 의식한 내환원성 BaTiO3 세라믹스의 연구를 발표하였다. Fe족의 금속을 내부 전극에 사용하는 것을 전제로 한 연구이었으며, 환원성 분위기에소 소성해도 환원되지 않는 baTiO3세라믹스가 MnO첨가로 얻을수있다고 보고하였다
그 이후 많은 연구자가 내환원성 BaTiO3 세라믹 개발에 힘쓰게 되었다. 1975년에는 Burn과 Maher가 Mn을 도핑한 BaTiO3-CaZrO3 세라믹스를 CO-CO2의 환원 분위기 속에서 소성하여 절연저항이 높은 BME MLCC용 세라믹 유전체를 얻었다. 최근에는 내환원성 BaTiO3 연구의 전성기가 되었다. 1981년에는 Hageman과 Hennings가 Mn, Cr, Co와 같은 액셉터 이온의 도핑에 의해 내환원성이 뛰어난 BME-MLCC용 유전체를 얻을 수 있다고 보고하였다.
Sakabe 등은 Ba의 일부를 Ca로 치환하고, 다시 화학량론 조성보다 A 사이트 리치로 함으로써 내환원성이 뛰어난 세라믹 유전체를 얻을 수 있다고 보고했다. 1970년대에 내환원성 BaTiO3 세라믹스의 원형은 거의 완성에 이르렀다. 이러한 연구 성과를 바탕으로 1970년대 중반 미국에서 Centralab사가 Ni 내부전극 MLCC를 재빨리 시장에 출시하였다.
그러나 이 제품은 초기 특성이 매우 뛰어났지만 절연저항 수명이 매우 짧은 치명적인 결함을 드러냈다. 사용되기 시작한 지 반년도 지나지 않아 절연저항이 저하되어 회로에 큰 전류가 흐르고 급기야 쇼트되어 발화에 이르는 사고가 시장에서 빈발했던 것이다. 이 사고로 시장에는 Ni 알러지가 만연하게 되었다. 이 사고를 계기로 미국의 콘덴서 제조사는 Ni 내부전극을 포기하고 AgPd 내부전극 MLCC 개발로 크게 방향전환을 하게 되었다.
최근 일본에서는 3216타입의 Pd 내부전극 MLCC가 베어팁의 형태로 처음으로 민생용도로 채용되었다. 1977년에 발매된 마쓰시타전기의 페퍼라디오(Paper Radio)였다. 이를 계기로 표면실장기술의 진전과 더불어 Pd내부전극 MLCC가 본격적으로 확대되어 버렸다. 1980년대에는 Pd 내부전극 MLCC가 민생용도로 서서히 채용이 진행되었지만 Pd의 가격상승이 커, Pd 사용량 저감을 위해 내부전극의 박층화 노력이 활발하게 진행되었다.
전극 비용 문제는 MLCC에 가장 큰 과제였다. Pd의 가격은 1985년 전후로는 450~750엔/g였다. 당시, Ni는 0.6~0.7엔/g라는 점에서 Ni화 혹은 기술적 정확도가 높은 AgPd화의 움직임이 있었으며, 미국에서는 Ni의 실패 때문에 AgPd화가 진행되었고, 일본에서는 AgPd화와 Ni화가 모두 검토되었다. AgPd화의 경우에는 BaTiO3 유전체의 저온 소결화가 필요하여 BaTiO3+ 유리의 검토가 활발히 시도되었다.
그런 가운데 독특한 방법이 Rutt에 의해 1972년에 발표되었다.내부전극층에 카본페이스트를 인쇄하여 그린칩을 제작하고 소성 후 생긴 전극층의 공동에 나중에 용융한 Pb를 압입하는 것이었다.Pb는 가격도 낮고 융점도 낮아 제조하기 쉽다. 매우 좋은 아이디어였지만, 아쉽게도 제조의 안정성과 특성 불균형의 문제로 실용화되지는 못했다.
Yonezawa 등에 의해 발표된 납복합페롭스카이트 화합물 PMT-PT를 이용한 MLCC는 소결온도가 비교적 낮아 내부전극에 AgPd를 이용할 수 있었다.이 대용량 콘덴서는 수지 몰드가 된 대형 제품이 산업용으로 사용되어 갔다. 내부전극을 Pd에서 AgPd로 하는 흐름 속에서 PMN-PT 등의 납복합페로브스카이트를 유전체로 이용한 MLCC의 개발이 의욕적으로 진행되었지만, PbO를 함유하기 위해 습도에 약하거나 혹은 납의 용출과 같은 문제 때문에 베어칩이라고 한다.
베어칩 타입에서는 MLCC의 개발은 BaTiO3+ 유리와 AgPd 전극의 조합 및 BaTiO3와 Ni 전극의 조합으로 압축되었다. Pd 가격 급등도 있어 1980년대 후반부터는 수명이 짧은 Ni 내부 전극 MLCC에서도 유전체 층을 두껍게 해 수명을 길게 하고, 나아가 수지 몰드를 한 제품이 일본 업체로부터 서서히 시장에 투입되었다. 이와 같이 고가의 Pd로부터의 속박을 벗어나는 기술개발이 혼돈된 상황에서, 1987년에 Fujikawa등은 Ni-MLCC를 발표하였다. 구미 업체를 중심으로 한 Ni 알레르기가 만연한 상황에서, 유감스럽게도 이 발표는 사용자에게 받아들여지지 않았다.
신뢰성이 높은 것은 물론, 절연 저항의 수명 메커니즘에 관한 이론적 뒷받침이 요구되고 있었다. 이 시대, Pd-MLCC조차 X7R 특성은 BaTiO3에 Nb205-Co203을 복합 첨가한 재료가 TAM 세라믹스사에서 독점적으로 나오고 있을 뿐이었으며, 시장에서는 일반적이지 못하였다. X7R특성같은 온도에 대한 정전용량의 변화율이 작은 MLCC로의 니즈는 강하게 존재했지만, 소거법에서 온도에 대한 안정성은 낮으나 정전용량이 큰 Y5V특성이 시대의 주류가 되었다.
절연저항의 수명에 대한 이론적 해명이 이루어지지 않은 상태였지만, Saito 등은 1990년에 Ho 첨가에 의해 신뢰성이 높은 X7R 특성의 Ni-MLCC를 보고하였다. 또한 1993년에는 Shizuno가 마찬가지로 Ho 첨가에 의해 Y5V특성의 Ni-MLCC를 보고하였다. 1990년에는 Nomura가 희토류 산화물의 첨가, 재산화 어닐링 및 입계 화학의 제어에 의해 절연 저항의 수명이 매우 긴 고신뢰성 Ni-MLCC를 보고하였고, 1992년과 1993년에는 절연 저항의 장수명화에 관한 메커니즘을 보고하였다.
희토류 산화물의 첨가, 재산화아닐 및 입계 화학의 제어에 의해 절연 저항의 수명이 매우 길어 Pd-MLCC에 필적하는 고신뢰성 Ni-MLCC가 가능하게 되었다. 이에 따라 Ni-MLCC는 서서히 알레르기가 강했던 미국 제조업체도 포함하여 1992년경부터 고신뢰성 Ni-MLCC는 점차 채택되었다. 오늘날에는 전세계에서 생산되는 MLCC의 95%이상이 Ni내부전극으로 되어있는 일본 기술자들의 포기하지 않는 대처가 성공으로 이어진 사례이다.
그 후, 요네다들은 1997년에 저온 소결의 고 Q를 가진 Cu 내부 전극 MLCC를 발표하였다. 이것은 어디까지나 높은 품질계수를 얻기 위해 도전율이 높은 Cu를 내부전극으로 이용한 것이지만, 상유전체로 내환원성이 높은 세라믹 재료였기 때문에 Cu 전극을 실현할 수 있었다. 이 기법은 고유전율계의 BaTiO3계 유전체 재료에 적용할 수 없기 때문에 Cu 전극은 포스트 Pd 전극이 되지 않고 고주파용 일부 MLCC에 채용되는 데 그치고 있다.
'2020-적층세라믹콘덴서의 재료-제조-실장기술과 최신기술' 카테고리의 다른 글
제2장1절 구조와 재료 (0) | 2022.05.07 |
---|---|
제1장4절 소형화 박층화 다층화 (0) | 2022.05.02 |
제1장3절 특성과 특징 (0) | 2022.05.02 |
제1장2절 시장동향 (0) | 2022.05.02 |
제1장1절-2 내부전극 (0) | 2022.04.30 |