2022. 5. 2. 22:39ㆍ2020-적층세라믹콘덴서의 재료-제조-실장기술과 최신기술
제1장 MLCC의 개요
제 4 절 소형화, 박층화, 다층화
1항 소형화
Class 2-MLCC 최대의 특징은 소형으로 대용량 즉 단위 부피 중 용량밀도가 높다는 것이다. 이 때문에 비교적 용량이 큰 캐패시터를 회로 기판 내의 한정된 공간에 많이 실장하는 것이 가능하다. 그림 1에 1990년부터의 시장에서의 MLCC형상 트렌트를 나타내었다. (2020년 이후는 예측치). 2004년경부터 가장 많이 사용되기 시작한 1005사이즈(1.0mm x 0.5mm x 0.5mm)는 스마트폰이 등장한 2007년경부터 구성비율이 늘어나지 않아 2010년 이후에는 감소세로 돌아섰다.이를 대신하여 사용하게 된 것이 보다 소형인 0603 형상(0.6mm x 0.3mm x 0.3mm)이며, 2020년의 현시점에서 가장 구성 비율이 높은 형상이 되어 있다.
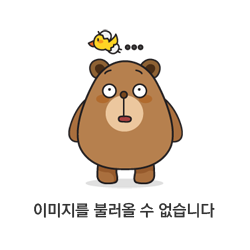
최근에는 휴대기기나 웨어러블 기기에서 부품의 고밀도 실장화 요구를 배경으로 한층 더 소형의 0603 형상(0.4mm x 0.2mm x 0.2mm)의 사용도 늘고 있으나 0402 형상 채용도 꾸준히 늘어날 것이다. 또한 초소형 MLCC, 예를 들어 0201 형상 (0.2mm x0.1mm x 0.1mm)의 제품도 고성능 스마트폰이나 소형 웨어러블 디바이스와 같은 소형 경량을 추구하는 전자 기기에서의 채용이 진행될 것으로 예측된다.
이처럼 MLCC의 소형 대용량화가 급속히 진행된 이유는 단순히 소형 부품 요구 증가만이 아니다. MLCC 메이커측의 비용 구조에도 이유가 있다. 동일 용량의 MLCC를 소형으로 할 수있는 것은 제조 비용의 저감을 가능하게 하는 것이다. MLCC 제조 프로세스에는, 어느 정도의 크기의 판상 적층체를 만들고 그것을 잘라서 작은 조각으로 분할하지만, MLCC가 소형이 되면 하나의 적층판으로부터의 「만들어지는 개수」가 비약적으로 증가한다. 또한 단위 제품당 필요한 유전체 원재료도 적어진다. 이 수량 이점을 활용하여 "용량을 변경하지 않고 MLCC 크기를 소형화한다"는 회로 설계자로부터 본 부가가치를 향상시키면서도 MLCC 가격의 증가를 최소한으로 억제하는 것이 가능했습니다. 이것이 MLCC를 소형 제품으로 대체하는 이유 중 하나입니다. 다만 용량을 유지한 소형화에는 Ni전극의 부자재비나 설비개발비가 부과되는 등 비용이 높아지는 요소도 있어, 수량 효과만으로 저비용화를 실현할 수 있는 것은 아님에 유의해야 한다
2항 박층화
MLCC의 용량밀도 향상은 주로 유전체 시트의 박층화에 기인한다. 유전체층이 얇아지면 한정된 형상 안에서 적층할 수 있는 매수를 증가시킬 수 있다. 병행평판 콘덴서의 정전용량은 잘 알려진 바와 같이 다음 식으로 표현된다.
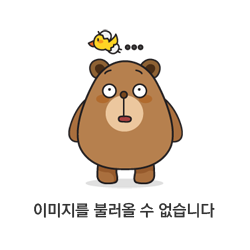
여기서 C는 정전용량, ε0와 εr는 각각 진공의 유전율과 유전체의 비유전율, n은 적층수, A는 한층당 전극면적, d는 유전체층의 두께이다.이 식에서 알 수 있듯이 유전체층 두께의 감소에 의해 적층수 n이 증가한다면, 1/d와 n의 상승효과로 용량이 크게 증가한다. 또한 전극 두께의 감소도 용량 증가에 기여할 수 있다. 전극의 두께는 상기 식에 포함되지 않아 직접적으로는 용량 증가에 기여하지 않는다. 그러나 전극이 얇아지면 그만큼 유전체층을 더 쌓을 수 있게 되므로 결과적으로 n의 증가에 기여하는 것으로 용량 증가를 가져오는 것이다. 이처럼 MLCC 소형 대용량화의 역사는 기술적으로는 유전체와 전극의 박층화 역사이기도 하다.
그림2에 Class 2 소형 대용량 MLCC에서의 유전체와 전극 층 두께의 연도별 추이를 나타낸다. 2000년대 초까지의 박층화 진행속도가 매우 큰 것은 이 시기의 소형 부품에 대한 요구가 급속히 높아졌기 때문이다.예를 들어 1990년대 후반에는 휴대전화가 보급되기 시작했고, 2000년대에 들어서자 3G에 따른 휴대전화의 고기능화와 플라스틱 관텔레비전에서 평면 TV(액정, 플라스마)로의 이행이 진행되었다.
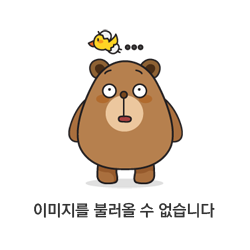
이 흐름은 2007년 이후 스마트 폰 시대가 되어도 계속했고 여기에 대응하고 유전체와 전극의 박층화도 멈추지 않고 진행되고 있다. 유전체의 박층화하기 위해선 제5장 1절에 서술하는 것처럼 얇고 평활하게 유전 분체를 깐 유전체시트를 형성하는 기술이 필요하어, 더욱이 이를 위해서는 원료로서 수 10~200nm정도의 미립의 구형 분체가 필수적이다.
한편 소형 대용량 MLCC의 주 원료인 BaTiO3(BT)에서는 일반적으로 입경이 작을 수록 정방성이 떨어지고 소결이 불안정(이상 입자 성장의 발생 등의)한 문제가 있다. 그러나 BT합성 기술과 소성 기술의 발달로 이 문제는 어느 정도 해결됐고 현재는 100nm정도에서도 높은 정방정성을 가진 BT가 양산할 수 있게 되었다.
이런 하이 그레이드한 분체 합성 방법은 제2장을 참조하기 바란다.따라서 유전체층의 박층화는 소경 BT 합성기술 박층시트 형성기술 및 소성기술이 발맞춰 진화해야만 진행시킬 수 있다. 그림2에서 최근만큼 진화의 성장이 둔화되고 있는 것은 요구되는 두께가 매우 작아져 이 보조를 맞추는 것이 어려워지고 있다는 것을 의미한다.
유전체 박층화와 비교해 완만하지만 전극 두께도 마찬가지로 해마다 박층화가 진전되고 있다. 이는 유전체와 마찬가지로 미립 Ni분말를 얇고 평활하게 패터닝하는 기술의 진화에 의한 점이 크다. 단 유전체와 다른 점은 전극의 경우 박층화시키면 소결 과정에서 전극면에 많은 구멍이 생겨버린다는 문제를 갖는 점이다. 이는 Ni 소결온도(700~1000°C)가 유전체 소결온도(1,100~1,300°C)에 대하여 낮기 때문에 유전체를 치밀한 세라믹으로 만들어 구워냄으로써 내부전극은 항상 과소결의 조건에 놓이기 때문이다. Ni 전극은 과소결이 되면 끊어져 구상화하려는 거동이 나타나게 된다. 이렇게 전극에
구멍이 뚫리면 전극 면적 감소에 따른 용량 손실, 소결 중의 층갈라짐(딜라미네이션), 전계 집중에 의한 장기 신뢰성 저하 등과 같은 다양한 불량이 발생하기 쉽다. 이 때문에 전극의 박층화는 쉽지 않으며 현재 최첨단 MLCC에서는 전극 두께가 유전체 두께와 비슷하거나 경우에 따라서는 유전체가 얇은 상황이다.
3항 다층화
MLCC의 다층화는 유전체와 전극의 박층화에 의해 실현되었는데, 이는 앞서 기술한 바와 같이 같은 용량을 보다 작은 형태로 달성시킨다'는 목적에 의한 것이 크다. 한편 비교적 대형인 MLCC, 예를 들어 4532형상 4.5mm x 3.2mm x 3.2mm)에서는 박층화 • 다층화를 진행시킴으로써 '전해 콘덴서 수준의 대용량을 달성하고, 전해 콘덴서를 MLCC로 치환한다'는 목적을 가지고 있다.
원래 MLCC는 전해 콘덴서에 대해 저 ESR · 저 ESL이라는 특징을 갖는다 (1장 제 3절 참조) 때문에 소형 및 저용량으로 임피던스를 낮출 수 있는 특징이 있지만, 그래도 전해 콘덴서와 비교하면 용량치 자체의 라인업은 낮다. 그러나 비교적 대형인 MLCC이면 다층화에 의한 용량값 증가 효과도 크기 때문에 박층·다층화를 진행시켜 용량값을 전해 콘덴서와 경합하는 수준으로 끌어올릴 수 있게 되었다. 예를 들어 2018년에는 4532형상으로 1000층 이상 적층함으로써 l000uF의 X5R 특성MLCC(그림3)가 양산되었으며, 이를 통해 전원회로의 콘덴서를 올 세라믹(All Ceramic)화 할 수도 있다.
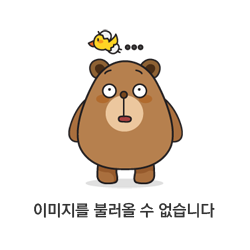
'2020-적층세라믹콘덴서의 재료-제조-실장기술과 최신기술' 카테고리의 다른 글
제2장2절-1 티탄산 바륨의 원료-산화티탄 (0) | 2022.05.07 |
---|---|
제2장1절 구조와 재료 (0) | 2022.05.07 |
제1장3절 특성과 특징 (0) | 2022.05.02 |
제1장2절 시장동향 (0) | 2022.05.02 |
제1장1절-2 내부전극 (0) | 2022.04.30 |