(Pressing)분무건조법을 이용한 세라믹 Powder의 조립화
1. 서론
일반적인 세라믹 제조공정에서 성형공정은 최종소결체 물성에 큰 영향을 미치며, 세라믹스의 각종 성형방법중, 가압성형법은 경제성, 양산성이 뛰어나고, 대형 성형체를 만들기 쉽고, 품질의 제어가 용이하다는 잇점이 있어 널리 사용되고 있다1,2). 이 가압성형의 전처리로서 조립공정은 필수불가결한 기술이다. 그 이유는 가압성형시 미분을 그대로 사용하면, 유동성이 적어 금형내 충진이 나쁘고, Lamination이 일어나기 쉽다는 결점이 있어 이를 극복하기 위해서 분말을 과립화할 필요가 있기 때문이다.
실제 성형시 과립이 갖추어야 할 가장 중요한 요소로서는
(1) 과립이 잘 흘러 Hopper에서 금형내로 균일하게 충진될 것(충진성)
(2) 금형내에서 과립이 압축될 때, 전달된 압력에 의해 과립이 완전히 파괴될 것(압력전달)
(3) 성형된 후 분말이 금형이나 Punch에 부착되지 않을 것(이형성)
이 3 요소가 건식성형에서는 매우 중요하며, 이 3 요소를 충족시키기 위하여 성형용 유기재료, 즉 결합제, 분산제, 이형제 등을 첨가하고 이를 조립화하는 것이 필요하다.
본고에서는 세라믹 분체의 조립화 방법으로 일반적으로 널리 사용되고 있는 Spray Drying법에 있어서 Slurry의 제조, Spray Dryer의 구성과 운전조건 및 과립의 평가에 대해 간략하게 기술하고자 한다.
2. Spray Drying이란
Spray Drying 이란 용액상태의 원료를 Spray Dryer의 고온 건조매체중에 분무시킴으로서 구형의 과립을 얻는 일련의 공정을 일컫는 말이다. 이때, 주입되는 원료의 상태는 Solution, Suspension 혹은 Paste 상태면 모두 처리 가능하며, 공정도 다른 건조방법에 비해 매우 간단하며 연속 대량생산에 적합하여 세라믹 뿐만 아니라 모든 공업에 폭넓게 이용되고 있다3,4,5).
습식분쇄된 원료를 조립화하는 공정은 그림 1과 같다. 그림에서 보는 바와 같이 원료분말과 결합제,분산제, 이형제 등이 혼합된 Slurry를 열풍중에 액적상태로 분무.건조하여 과립을 제조하게 된다. 이러한 조립공정을 단계별로 나누어 보면 Slurry의 제조, Spray Drying 및 과립의 평가로 대별할 수 있다.
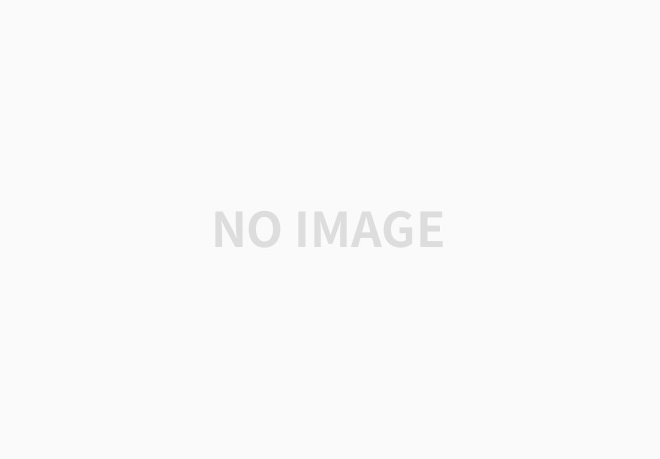
그림1. Spray Drying공정
3. Slurry의 제조
3.1 Spray Drying에 사용되는 Slurry제조용 유기 첨가제
Spray Drying을 성공리에 수행하기 위해서는 분산성이 양호하고 안정된 Slurry의 제조가 필수적이다. Slurry는 Water Content가 20 ~ 50 %로서 분산성이 양호하고 안정된 Slurry를 얻기 위해서 결합제, 분산제, 및 윤활제등을 첨가하게 된다. 과립에 필요되는 기능을 부여하기 위해 첨가되는 유기첨가제는 다음 표1과 같이 분류된다6).
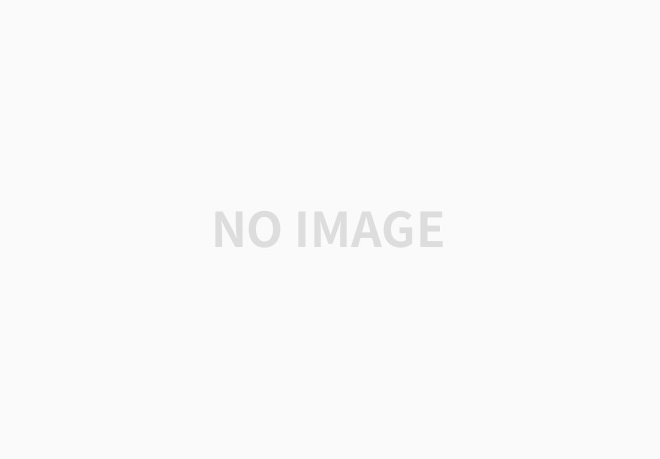
1) 결합제: 성형체가 소성되기 전까지 Handling에 견딜수 있는 Green 강도와 가소성을 부여할 목적으로 사용된다.
2) 가소제: 표 1에 나타낸 기능을 부여하기 위해 이용되며 결합제중에도 이 기능을 갖는 것이 있다
3) 윤활제: 표 1에 나타낸 기능 외에 이형을 쉽게하고 금형의 수명을 길게 하는 기능을 가진다
4) 분산제: Slurry의 안정성을 유지하기 위해 사용한다.
성형체를 소성하였을 때, 첨가제가 소결체중에 잔류하지 않아야 하며 첨가제의 분해나 연소가 급격히 일어나지 않고 Smooth하게 제거되야 한다는 것이 선택조건중 하나이다. 세라믹 분체의 종류, 입경이나 입도분포에 따라 첨가제의 종류나 첨가량을 실험적으로 선택해야 하며, 보통 분체중량에 대해 2 ∼ 4 % 첨가한다.
(1) Binder
Binder란 본래 결합제만을 지칭하였으나, 최근에는 활제, 가소제등을 포함한 복합계의 결합제를 의미하기도 한다. 일반적으로 복합계의 결합제를 Binder라고 칭하는 경우가 많으나, 보통은 결합제의 의미로 사용되고 있다. 결합제를 선택하는 조건은 다음과 같다7,8).
① 될 수 있는 한, 소량첨가로 효과가 있을 것
② 분체와 반응하지 않을 것
③ 물 또는 용매에 잘 녹아 Emulsion으로 투입가능할 것
④ 산화, 비산화분위기중 비교적 저온 (300 ~ 400 ℃)에서 완전히 분해 휘발할 것
⑤ 분해 휘발한후 회분은 0일것, 혹시 약간 (ppm 단위)남더라도 알카리류 (Na, K)이나 중금속 (Fe, Ni, Co, Cr)성분을 함유하지 않을 것
⑥ 분해가스가 독성이나 강산, 강알칼리성이 아닐 것
⑦ 습기에 민감하지 않을 것
결합제의 종류를 크게 나누면 수계 결합제와 용제계 결합제로으로 구별된다. 주로 수계 결합제 중에서는 PVA(Poly Vinyl Alcohol), PEG(Poly Ethylene Glycol), MC(Methyle Cellulose)등이 널리 사용되고 있으며, 최근에는 PEO, 아크릴계가 주목받고 있다. 또한 왁스중의 마이크로 크리스탈린 왁스등은 가소성이 강하면서 점착성을 유지하고 있어 Electronics분야에서 IC기판등의 결합제로서 사용되고 있다.
용제계 결합제 중에서는 EC(Ethyl Cellulose), PVB(Poly Vinyl Butyral)등이 주로 사용되고 있으며, 최근에는 수계에도 응용가능한 아크릴계가 주목받고 있다. 표 2에 결합제의 종류를 나타내었다9).
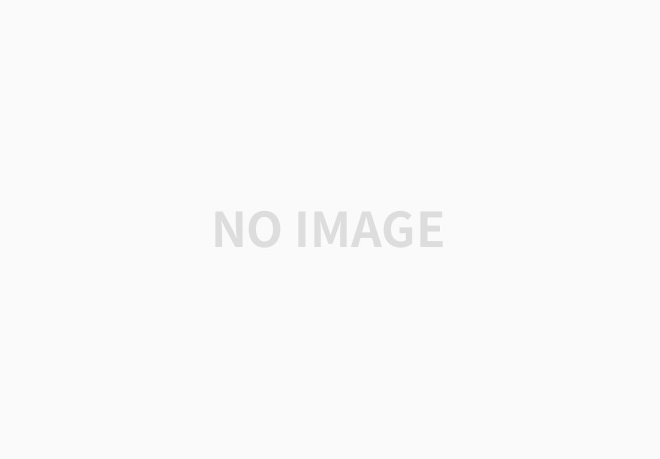
결합제 첨가시 주의할 점으로는
① Emulsion 상태로 첨가하는 것이 바람직하나, 결합제용액을 많이 저으면 안정한 기포가
생기게 되고, 이 기포가 과립 내부에 Hole을 형성하여 밀도를 저하시키게 된다. 그러므로
교반시는 저속 믹서를 사용해야 한다.
② 결합제 첨가량이 많으면 탈지공정에서 문제가 생기거나 과립이 딱딱하게 되는 반면,
첨가량이 적으면 성형체 강도가 떨어지게 되므로 고형량의 0.5∼4.0%를 첨가하는 것이
바람직하다.
③ 성형시에 금형내 최밀충진을 하기 위해서는 과립밀도가 중요하며, 이는 고형량이 높을
수록 양호하므로 Slurry의 점도를 가급적 낮게 유지시켜 주는 결합제를 선택해야 한다.
④ 결합제는 분산매에 입자를 충분히 분산시킨후 투입시키는 것이 바람직하다. 바인더를 초기
에 투입하면 점도가 상승하고 결합제가 적절한 분쇄 및 혼합을 방해하므로 좋지 않다.
(2) 가소제
가소제는 적은 힘으로 영구변형을 일으키는 성질로 결합제에 첨가하여 결합제의 유리전이온도(Tg)을 저하시키고, 부드럽게 하여 성형을 용이하게 한다. 수계에서의 대표적인 가소제는 글리세린, PEG 등이 있으며 용제계에서는 부탈산에스테르가 있다.
Spray Drying에 사용되는 결합제와 가소제의 예를 표 3에 나타내었다6).
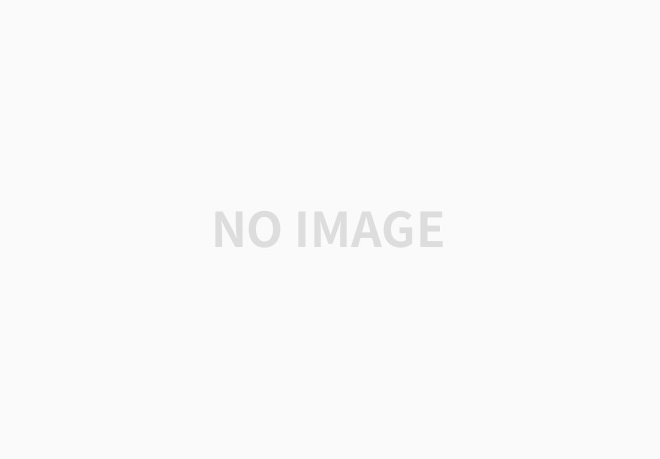
(3) 분산제
Slurry를 제조하는 제 1단계는 용액에 분말을 분산시키는 것이다. Spray Drying에 있어서 Slurry의 고형량이 많을 수록 경제적 측면에서 유리하며, 고형량이 높을 수록 과립제조량이 많아진다. 그림 2에서 보듯이일반적으로 고형량이 50 wt%에서 75 wt%로 증가하면 과립제조량은 3배 증가한다. Slip에 첨가되는 분산매양은 Powder의 입도분포, Particle 형상과 밀접한 관련이 있다. 따라서 고형량을 높이면서 Slurry의 점도를 낮추는 것이 공정상의 주요한 Factor로 작용한다.
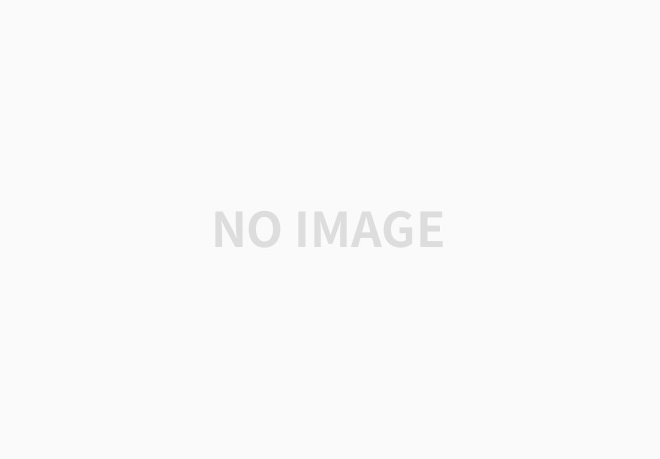
1) 수계에서의 분산
보통 Slurry중의 분말은 직경이 수 μm의 입자로 이루어져 있으므로, Slurry는 콜로이드 분산으로 간주할 수 있다. 콜로이드의 안정에 관한 이론은 1940년대의 Dejaguin, Landau, Verwey, Overbeeck이 발전시켰으며 보통 DLVO이론이라 부른다. 이는 Suspension에서의 입자간에 작용하는 힘, 즉 Van der Waals인력과 정전기적 척력간의 상대적 차이로서 콜로이드의 안정성을 평가하는 이론이다10.11).
세라믹 Slurry에서의 입자간 상호작용력(VT)은 입자간의 인력(VA)과 척력(VR)의 합으로서, 입자간 거리의 함수이다. 해교된 Slurry의 경우, Slip 내에서 입자가 서로 접근함에 따라 두 입자간의 전기이중층이 겹치게 되면 척력이 인력을 극복하게 되어 입자는 분산되고, 이 때 상호작용력이 (+)값을 갖는다. 한편 응집되어 있는 Slurry는 (-)값을 갖는 데, 이는 입자의 표면전하가 중성을 띠어 전기이중충이 붕괴되면서 Van Der Waala인력이 척력보다 커짐을 의미하며 이로써 입자가 응집한다. 계의 분산도는 입자간 상호작용력으로 결정되며 입자간 거리에 따른 상호작용력을 그림 3에 나타내었다
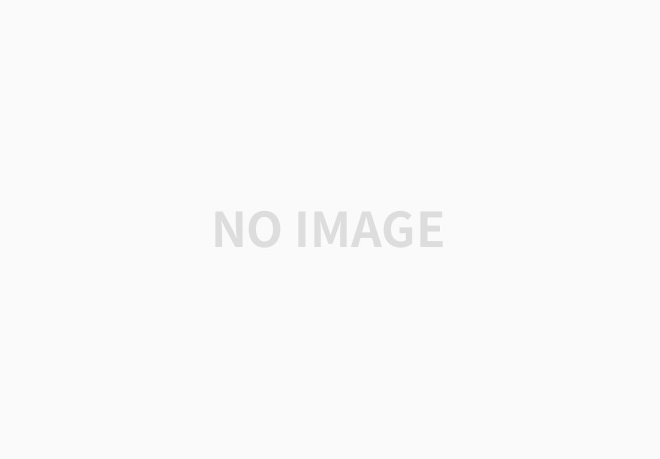
어떠한 Suspension에서도 인력(VA)은 일정하므로 Potential Energy합의 곡선모양은 척력(VR)에 의해 결정된다. 그러므로, 계의 분산안정성은 척력(VR)을 조절하는 변수, 즉 입자표면의 하전과 이중층의 두께의 함수이다. 따라서 수계 Slurry의 분산은 전기이중층의 Electrical Potential을 변화시키는 분산제에 의해 조절될 수 있다.
2) 용제계에서의 분산
수계의 경우에는, 분산에 대한 하전기구(charging mechanism)가 (1) 물에의 이온화종의 해리와, (2) 입자표면위에 이온의 선택적인 흡착이라는 두단계로 이루어 진다. 반면 용제계의 경우에는, 분산에 대한 하전기구가 그림 4와 같이 (1) 염기성 표면위에 산의 흡착, (2) 표면으로 양자 (proton) 를 양자의 이동에 의한 흡착된 산의 해리, (3) 해리된 음이온이 용액에 용해되고 입자표면은 (+) 전하를 띠게 되는 공정으로 이루어 진다. 그러나, 용제계의 정전기적 반발력은 수계에 비해 훨씬 작다. 왜냐하면, 용제가 물에 비하여 낮은 이온농도와 유전상수를 갖기 때문이다. 그러므로, 용제계에서의 분산은 입체 안정화 (Steric Stabilizaton) 가 유효하다. 따라서, 용제계에서는 보통 입자에의 흡착층을 크게하는 고분자량의 분산제를 사용하며, 특히 입자가 작아질 경우 Wetting성 및 안정성을 향상시키는 분산제를 함께 사용하는 것이 좋다. 보통 수계에서는 비이온활성제, 용제계에서는 오레핀산 글리세린이나 아민계 활성제가 일반적으로 사용된다.
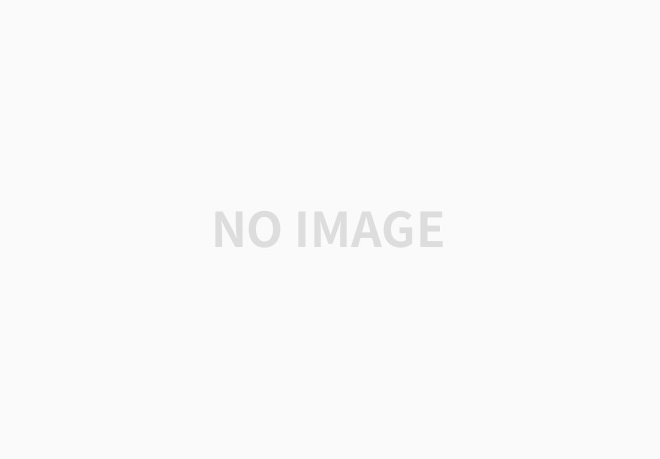
분산제는 용도에 따라 수계 및 용제계로 분류되며 그 종류는 표 4와 같다12).
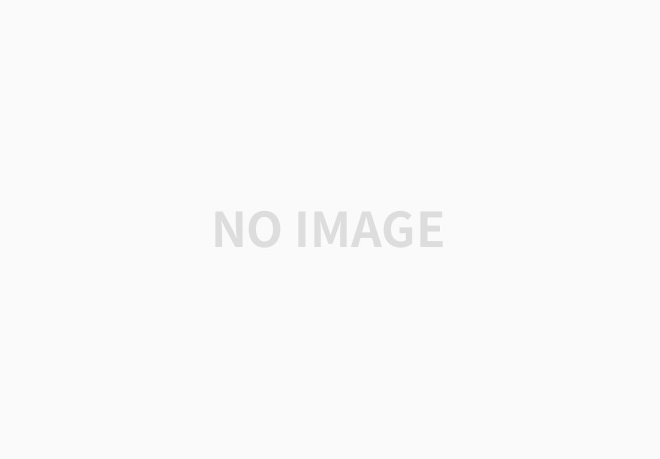
3.2 Slip의 물성평가
Slip의 물성은 다음 항목으로 결정될 수 있다.
① Slip의 밀도 (DA)
② Foam 함량 (= 100(DT-DA)/DT ,DT= Slip의 이론밀도)
③ 고형량
④ 점도
바람직한 Slip은 밀도와 고형량은 높을수록, Foam함량과 점도는 낮을수록 좋다.
4. Spray Drying 공정 구성 및 운전조건
4.1 Spray Drying의 구성
분무건조 Process는 그림 5에 나타낸 4개 단계, 즉
① Atomization (미립화)
② Slurry - Air Mixing (기액혼합)
③ Evaporation (증발)
④ Dried Powder Recovery (분체회수)
로 나누어 생각할수 있다. 그럼 각 단계별로 나누어 기기의 구성을 알아보자.
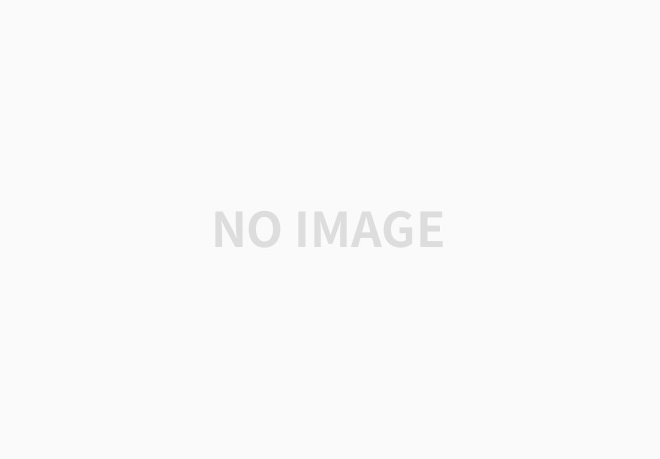
(1) Atomization (미립화)
분무건조법으로 얻어지는 분말의 입도는 거의 미립화시의 액적입경에 지배되므로 미립화, 특히 분무기의 선택과 설계가 중요하다. 분무기로서는 Centrifugal Type (Rotary Wheel or Disc)과 Pressure Nozzle Type이 일반적으로 표 5에 Two Fluid (Pneumatic) Nozzle과 함께 비교하였다13).
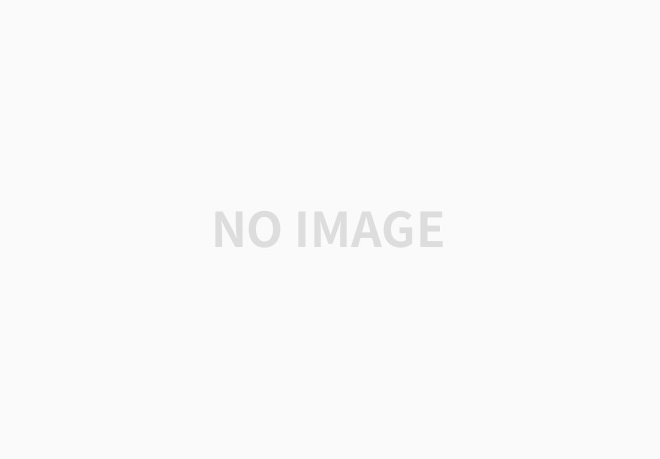
1) Rotary Atomizer
고속으로 회전하는 원반의 중심에 액적 을 공급하면 원심력에 의해 원반의 주변 에서 미립화 된다.
장점으로는
① Slurry 운송시 고압펌프가 불필요
② 적정 입경을 조절하는 것이 용이
단점으로는
① Chamber Diameter가 커야하며
② Atomizer 가격이 비싸다.
액적의 입도분포는 대수확률분포를 나타내며 평균입경은 다음 식과 같다
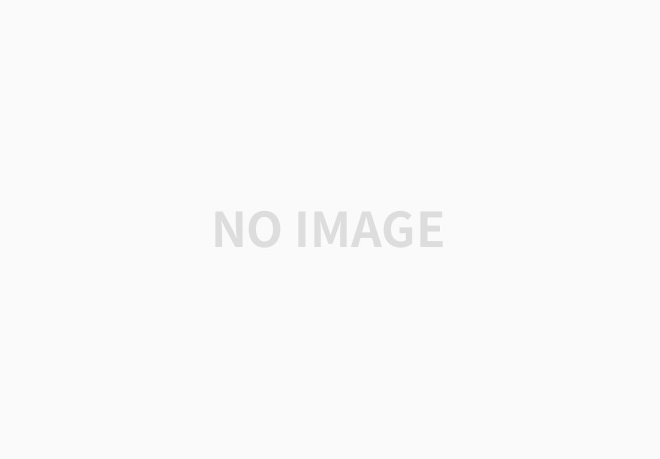
즉, 입경은 Feed Rate, Viscosity, Surface Tension에 비례하고 Rotation Speed와 Drolet Diameter에 반비례한다. 또한 입경을 조절하는 Key Factor는 Atomizer의 회전속도이다.
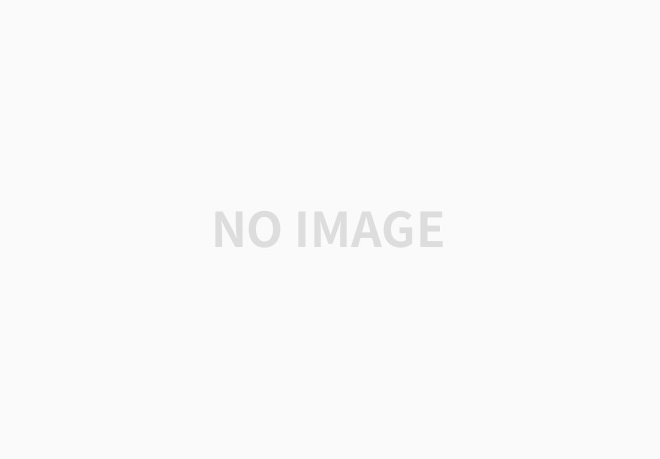
2) Pressure Nozzle Atomizer
Slurry가 Feeding될 때 압력을 가하여 분무시키는 Atomizer로 분무 Pattern에는 Hollow Cone과 Solid Cone이 대표적이 다. 동일 분무압력에서 미립화 특성이 뛰어난 Hollow Cone이 폭넓게 사용되고 있다.
장점으로는 과립의 입경이 120~250μm로 입도분포가 좁고 단점으로는
① 고압펌프가 필요로 하며
② 고압 조절기술이 필요로 하며
③ Wall-Sticking이 발생한다
평균입경은 Orifice diameter, 점도에 비례하며, Feeding Pressure에 반비례 하며, 평균입경은 다음 식과 같다
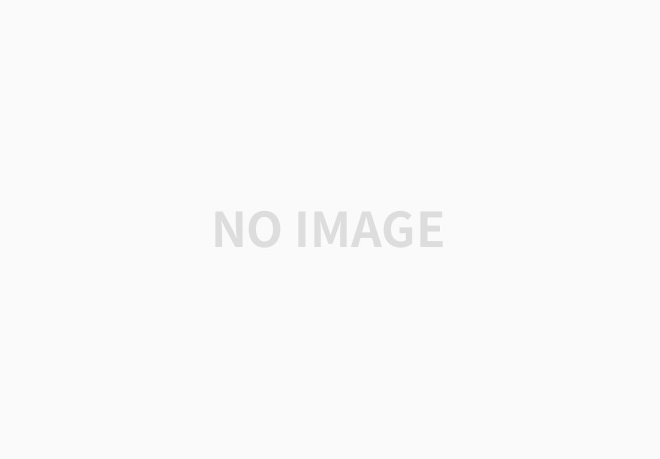
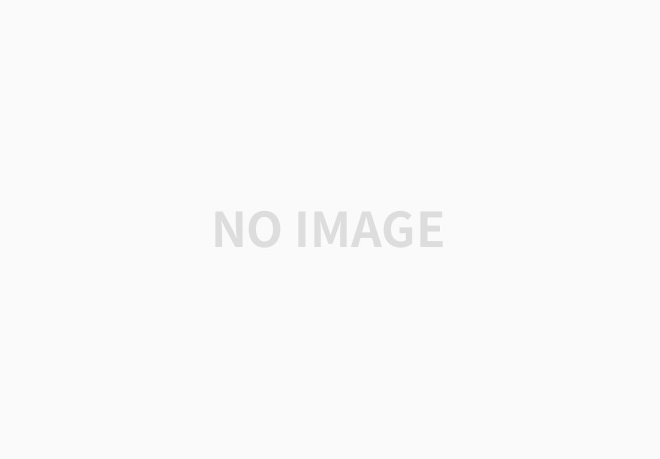
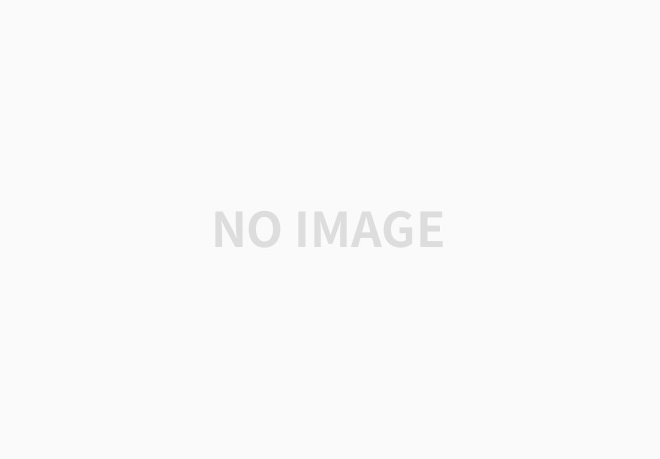
평균입경을 조절하는 Key Factor는 Orifice에서의 압력구배이다.
3) Two-Fluid Atomizer
Slurry에 고속의 기류를 가하여 분무시 키는 Atomizer로 Air Mixing방법에 따라
① Internal Mixing,
② External Mixing
으로 분류한다.
주로 고점성유체의 미립화에 사용되며 실험실 Scale에서 사용하는데 용이하다. 단점으로는 용량이 작고 가격이 비싸며 입도분포가 넓다
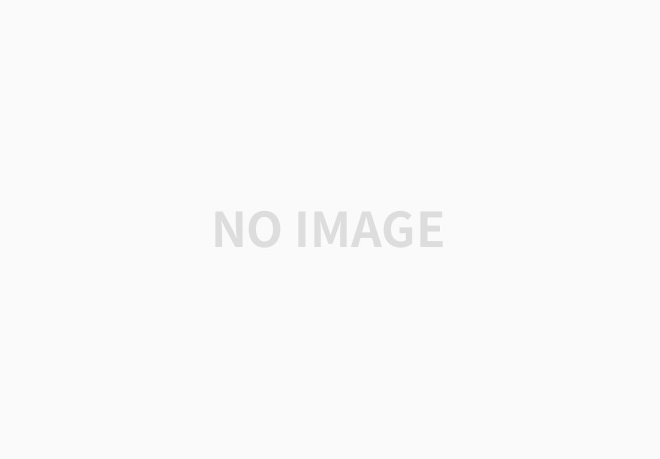
평균입경은 다음 식으로 주어진다.
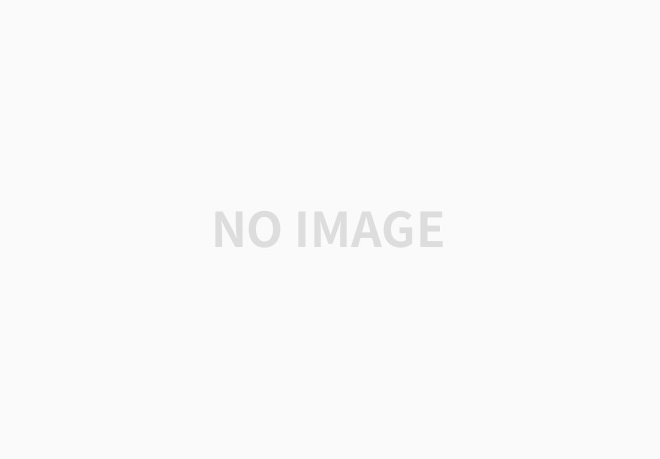
평균입경을 조절하는 Key Factor는 Slurry에 대한 Air의 Mass Flow Ratio 이다.
(2) Slurry - Air Mixing
분무건조장치는 주로 액적과 열풍과의 접촉방식에 따라 크게 3가지로 분류되며 Drying Chamber내의 열풍의 흐름은 액적 건조시간, Chamber내의 잔류시간, 수분증발등에 밀접한 관련이 있다.
1) Co-Current 방식
분무액적이 열풍과 함께 Chamber 정상에서 Chamber내를 하강하는 Type으로 최초는 고온의 열풍과, 건조가 진행됨에 따라서 저온의 열풍과 접촉한다. Atomizer는 Rotary와 Pressure Nozzle Type 모두 사용가능하며 Rotary Atomizer의 경우가 일반적으로 더 많이 사용된다.
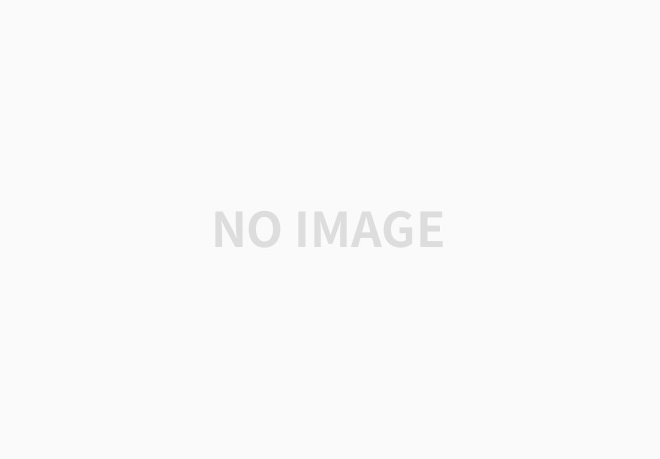
2) Counter-Current 방식
액적이 가압노즐을 통해 미립화되어 Chamber 상부에서 Chamber 하부로 열풍은 Chamber 하부에서 도입되는 방식으로 액적은 초기에 차가운 Air와 접촉하여 액적의 수분이 감소하면서 후기에 열풍과 접촉한다. 큰 입자의 건조에 적당하고 열효율이 높으므로 분말세제의 제조에는 거의 이 방식을 채용하고 있다
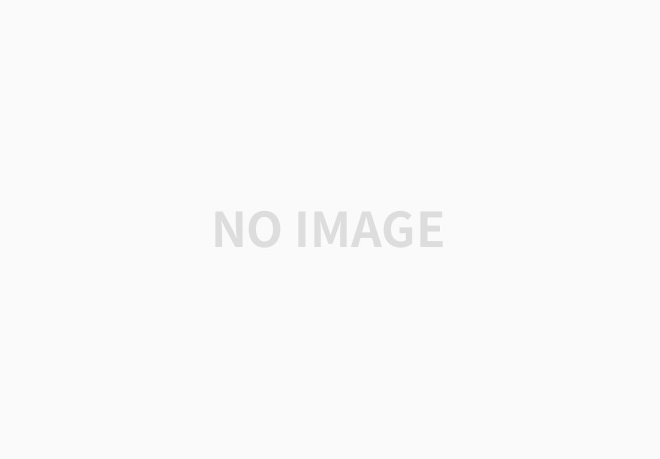
3) Mixed Flow
열풍은 Chamber 상부에서 아래쪽으로 도입되고 액적은 Chamber하부에서 가압노즐을 통해 위로 향하여 분무되어 초기에는 열풍과 반대방향으로 접촉후 중력에 의해 낙하한다.
이방식은 Chamber내 입자의 대류시간이 길게되어 작은 Chamber 내에서 큰 액적 건조에 적합하다.
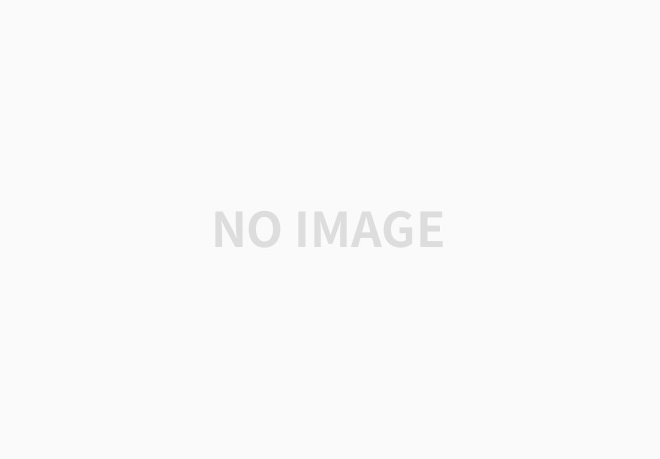
(3) Chamber 내에서의 액적이동
Chamber 내에서 액적의 이동은 다음 3단계를 거치면서 이동하게 된다.
제 1단계 : Atomizer로 부터 액적 방출
제 2단계 : 액적의 감속
제 3단계 : 자유낙하 혹은 Chamber내의 열풍흐름에 의한 운동
(4) 건조과정 (Evaporation)
액적의 건조과정에서의 증발정도와 형상변화등의 특성은, Drying Chamber의 설계나 원액제조조건의 설정과 밀접한 관계를 갖는다. 증발은 재료의 특성에 따라 다르나 일반적으로 균질용액의 경우 표면 증발기간이 짧고, 건조의 진행에 따라 증발속도는 감소한다. 미립자의 현탁액의 경우도 함수율 30~50% 이하에서는 감율 건조특성을 보인다.
액적의 형상변화는 Charles Worth등이 그림 13과 같이 분류하였다14).
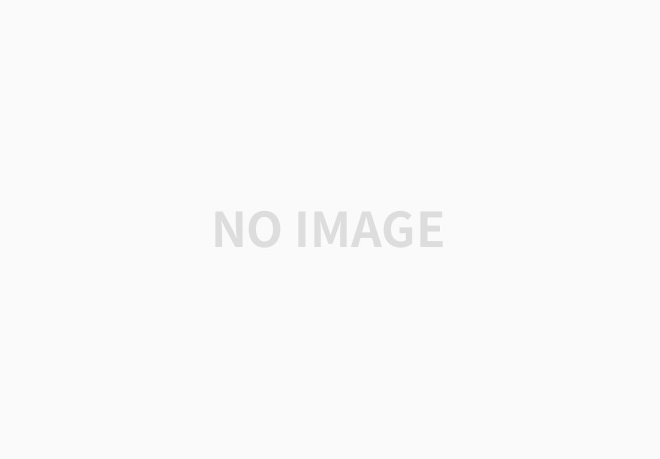
액적경은 표면증발기간에서는 건조진행에 따라 축소하여가고, 감율건조기간에서는 열풍온도, 재료특성에 따라 딱딱한 껍질을 형성하는것, 팽창하는 것등 6개로 분류된다. 그림 13에서는 건조공기가 용매의 끓는 점 이상일 경우와 이하의 경우로 나누어 액적 의 건조거동을 분류한 것이다.
건조재료를 3개로 크게 분류하면
① 식염, 염화 암모늄등과 같이 입자표면에 결정이 석출하여 딱딱한 껍질을 형성하는 재료
② 젤라틴, 탈지분유등과 같이 입자표면에 피막을 형성하는 재료
③ Bentonite 처럼 고형분과 수분이 분리되어 건조의 진행에 따라 액적경이 감소하는 재료
피막을 형성하는 재료에서는 열풍온도가 100 ℃ 이상의 경우 건조가 진행됨에 따라 액적 내부 증기압이 대기압보다 높아져서 액적이 팽창하는 현상이 나타난다. 100 ℃ 이하의 온도에서는 증기압이 낮으므로 액적경은 거의 변화하지 않는다.한편 껍질을 형성하는 재료에서는 액적 내부압이 높아지므로 껍질의 일부가 깨지기도한다.
Drying Chamber내에서의 액적건조과정은 다음 그림14에서와 같이 Slurry가 Chamber내로 투입(A-B구간)되어 증발이 최대한 발생한다. 그후 Drying Rate가 일정하게 되면서(B-C구간), Droplet의 온도는 낮게 유지되며 기본적으로 고정된다. 또한 Surface Saturation을 유지하면서 증발이 계속된다. 이 구간의 길이는 Droplet의 용매함량, Liquid점도, Drying Air온도 및 습도에 따라 달라진다. C점부터 Droplet Surface의 유지가 안되면서 증발율이 감소하기 시작하여 Droplet 의 표면온도도 증가한다. 더욱 진행이 되면서 액적 내부가 증발되 면서 액적이 Solid Crust에 둘러싸이며
그 이상의 증발은 껍질의 Permittivity에 따라 다르다.
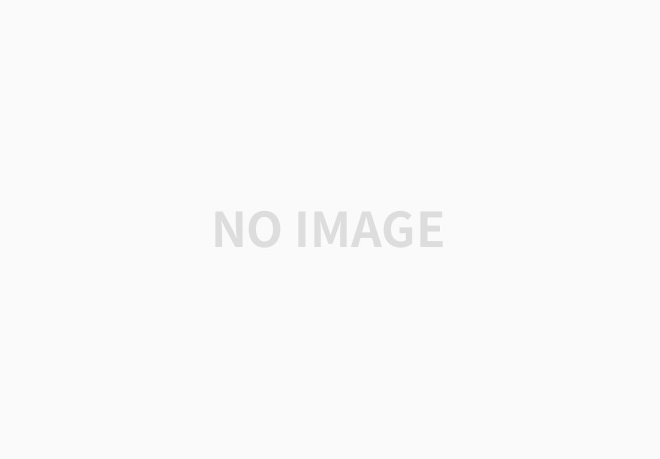
4.2 운전조건 및 공정상의 Trouble
과립의 성질을 좌우하는 조건으로는 ① Spray Dryer기종의 선정, ② 결합제의 선정 및 Slurry의 제조조건, ③ Spray Dryer의 운전조건을 들 수 있다. 이 중에서도 ①의 기종선정이 제일로 중요하며 이것이 잘못되면 ② 또는 ③의 조건을 수정하여도 결코 바람직한 과립을 얻을 수 없다. 일반적인 세라믹 분말의 조립공정에서는 분무기로는 Rotary Atomizer, Slyrry-Air Mixing방식으로는 Co-Current방식이 널리 사용되고 있으며 이 방식을 기준으로 각각의 조작변수에 따른 과립의 특성을 알아보면 다음과 같다.
(1) 입구온도 및 출구온도
입구온도 및 출구온도는 주로 과립의 수분함량과 관계있으며, 또한 과립의 겉보기 밀도와 관계깊다.입구온도가 높으면 액적의 건조가 빨라지고 따라서 겉보기 밀도가 낮다. 입구온도와 출구온도의 차가 작으면 과립의 수분량이 많아지며 겉보기 밀도가 높아진다. 또한 입구온도가 어느 정도 이상이면 분무 직후의 Slurry액적이 급격하게 건조되어 표면이 고화되면서 과립이 팽창하여 조립이 많아진다.
(2) 공급량
Slurry의 공급량은 과립의 입경 및 수분량과 관계있다. 공급량이 많아지면 과립의 입경은 증가하고 수분량도 증가한다.
(3) Atomizer 속도
Atomizer 속도는 주로 과립의 입경 및 입도분포와 관련된다. Atomizer 속도가 빨라지면 액적경이 감소하여 입경은 감소하고 입도분포도 좁아진다.
(4) 열풍의 흐름속도
열풍의 흐름이 빨라지면 Chamber내의 과립의 체류시간이 짧아져서 과립의 수분량이 많아진다. 또한 입구온도 및 출구온도의 차가 적어진다.
(5) Slurry농도 및 Binder량
Slurry의 농도가 높으면 Slurry의 점성이 커지고 따라서 분무된 액적이 커져 입경이 커지게 된다. 또한 Binder량이 증가해도 Slurry의 점성이 증가하므로 마찬가지 효과가 발생한다. 또한 농도가 낮으면 건조가 불충분한 채로 끝난다.
Spray Dryer의 운전중 발생하는 과립의 변형 및 Chamber벽에의 부착에 대해 알아보면 다음과 같다.
(1) 벽면 부착 (Wall Sticking)
Chamber벽에의 부착원인은 다음과 같이 세가지로 분류가 가능하다.
① 액적의 표면 고화전에 Chamber벽내에 액적이 접착됨
이는 액적크기가 크고 Atomization과 Air flow 조건이 부적절하며 고형량이 적을때 발생한다.
② 건조온도에서 과립 표면에 부분적으로 접착성있는 경우
③ 건조된 과립이 Chamber에 붙어 Dusting 층을 형성하는 경우
위의 조건중 ①항, ②항 모두 첨가제의 영향에 의한 것으로 과립의 형상은 유지가능하며 Soft한 부착층을 형성한다. 하지만 고온에서 지속적으로 노출되므로 열분해 및 증발양상이 변화하여 최종 분체의 Compaction 거동이 달라진다.
(2) 中空狀 과립
중공상 과립가 존재하게 되면 Spray Drying된 과립의 겉보기 밀도가 저하되어 최종 물성에 악영향을 미치는데, 中空狀 과립의 형성에는 4가지 원인을 들 수 있다.
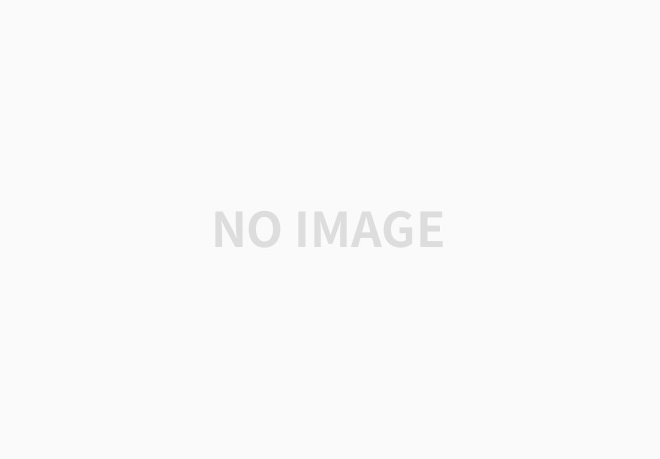
① 액적주변에 Elastic Film층이 형성되어 액적 온도가 증가함에 따라 증발율이 감소되므로 내부 수분이 증기화되면서 中空상 과립이 생성
② 용융성 염의 경우 액적표면에서 액체 증발 및 염의 결정화가 동시에 진행되어 증발율이 염의 확산속도보다 크므로 中空과립이 생성
③ 비용융성 염의 Slurry 경우, 액적표면의 액체흐름은 모세관 현상에 지배받으므로, 건조과정 종료 단계에서 내부에 부분적 진공상태가 이루어져 있어 과립이 붕괴되어 中空과립 생성
④ 초기 Slurry에 있었던 기포에 의해 中空 과립 생성
위의 조건중에서 ①번이 가장 유력한 Mechanism으로 Slurry 내의 고형량을 최대한으로 유지하는 것이 중공상 과립의 생성을 방지한다.
(3) Hard Granule 형성
Hard Granule의 생성은 액적내의 Binder의 이동과 밀접한 관련이 있다. 즉, 특히 수용성 Binder일 경우, 유기 Binder가 건조동안에 Binder Flow가 발생하며, 내부의 수분의 상당량이 액적 표면으로 이동할 때 Binder도 이동하게 되어 과립의 표면에 Binder 농도가 증가하게 된다. 고로 표면층이 딱딱하게 되어 가압후에도 과립이 파괴되지 않는다
Slurry내 고형량을 많게 하여 건조시간을 줄이면 이러한 Binder 이동을 억제할 수 있으며, 앞에서도 언급했듯이 Slurry의 고형량을 최대로 하면서 점도를 낮출 수 있는 Binder를 사용하는 것이 바람직하다.
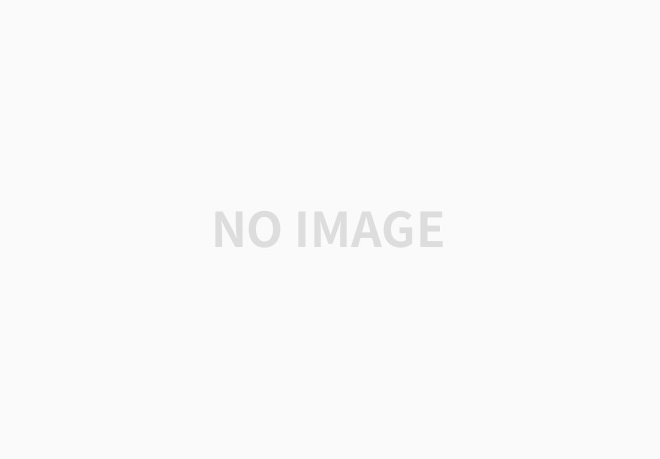
5. Granule의 평가
5.1 과립에 요구되는 조건
① 과립의 유동성이 클 것
즉 과립간의 마찰계수가 작고, 금형에의 충진이 용이해서 금형의 구석구석까지 흘러 들어가야 한다.
② 과립형상은 구상일 것
③ 과립의 입도분포가 좁을 것
④ 과립입도는 성형체의 크기에 맞출 것
⑤ 과립은 적당한 강도를 가질 것
즉, 금형에 충진하는 경우 lamination의 원인이 되는 미립자로 분리되지 않아야 한다. 또한 가압의 초기에 쉽게 파괴되지 않고, 우선 과립이 이동하여 최밀충진을 하고 과립간에 존재하는 공기가 빠져 나가기 쉬울 것
⑥ 가압의 중기에 과립이 파괴될 것
이 때 과립간의 공기는 빠져 나가고 가압이 완료되었을 때 분체가 결합할 수 있을 것
⑦ 과립의 밀도가 클 것
이는 위의 ①항, ⑤항의 필수조건으로 과립의 밀도는 직접 측정 할 수 없으므로 일반적으로 간접적인 방법으로 일정용적 또는 일정중량의 과립을 취하여 충진시켜 그중량 또는 용적으로 겉보기 밀도를 측정한다
⑧ 과립의 잔류수분이 적당할 것
과립의 수분이 지나치게 많으면 가압초기에 쉽게 파괴되어 위의 ⑤항을 만족시키지 못하고, 또 가압시에 금형에 점착하기 쉽다. 또한 수분이 지나치게 적으면 lamination이라는 층상의 크랙을 갖는 성형체가 발생하는 등 수분이 적당하면 이들 문제점이 쉽게 해결되고 가압이 완료된 후 분체가 충분히 결합하여 높은 성형밀도를 갖는 성형체 제조가 가능하다.
5.2 과립의 평가
과립은 다음과 같은 항목에 걸쳐 분석을 해야한다.
① 입도분포
② 유동성
③ 겉보기 밀도
④ 잔류수분량
⑤ 유기첨가제량
⑥ Compaction 거동
⑦ 미세구조
①, ②, ③ 항목의 측정은 ASTM B 212 - 82, B 213 - 83, B 214 - 86 에 정해진 방법으로 측정한다.
④ 및 ⑤ 항목은 TG - DTA로 측정하되 특히 유기첨가제양은 Slurry에 첨가한 양과 동일해야 하며, 유기첨가물량이 적게 측정되면 건조동안 부분적인 증발이나 열구배가 발생한 증거로 볼수 있다.
⑥ 항목의 조사 방법으로는 Compaction Curve를 작성해야 하며, 이는 가한 압력하에서의 성형체의 밀도 를 측정하여 (ASTM B 331 - 85) 압력과 성형체의 밀도변화를 그리면 그림17과 같은 Curve를 얻을 수 있다.
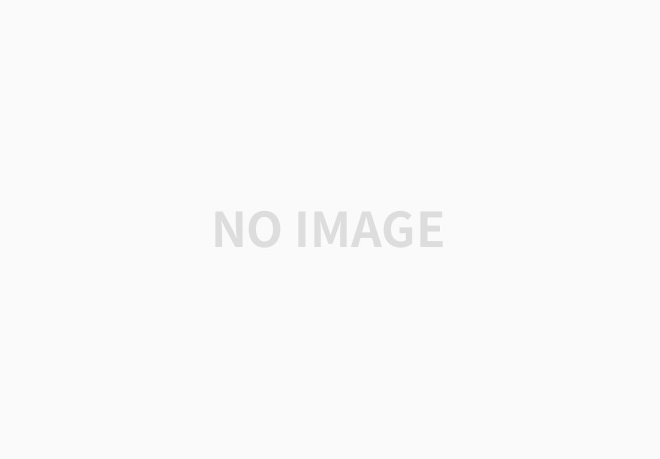
그림 17에서와 같이 성형 압력에 따라 성형단계를 3단계로 나눌수 있다. 1단계에서는 가압에 의해 과립이 미끄러져 재배열(Sliding & Rearrangement)된다. 여기서 Py는 겉보기 Yield Pressure로 이 압력하에서의 밀도증진은 통상 1% 미만이다. 이 단계에서 과립간 공극의 크기는 과립내의 평균기공 크기에 비해 매우 크다.
2단계에서는 Yield Pressure를 초과함에 따라 과립이 변형되거나 파괴된다. 따라서 공극의 체적이 급격히 감소한다. 이단계에서의 성형체 밀도는 과립의 변형 및 충진에 좌우된다.
3단계에서는 대부분의 과립간 기공이 사라지고 과립내의 입자가 미끄러져 재배열되므로써 성형체의 밀도가 과립의 밀도보다 더 커지게 된다.
그림 18은 성형중의 과립의 형상변화와 기공크기분포를 모식적으로 나타낸 것이다.
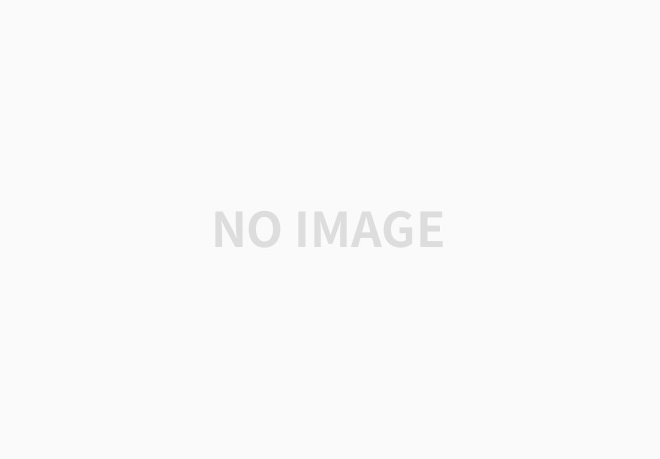
6. 결론
분무 건조법에 의한 세라믹 분말의 조립화에 관한 지금까지의 연구를 종합해 보면, 대별하여 1) slurry의 분산과 binder system, 2) binder system과 spray dryer의 운전 조건이 과립 특성에 미치는 에 미치는 영향, 3) 과립 특성이 성형성및 소결체에 미치는 영향등으로 정리되어 진다.
Spray Dryer 의 발달, 그리고 최근 세라믹 프로세싱의 중요성이 크게 부각되면서 Spray Drying 에 대한 연구가 활발히 진행되고 있으나, 아직도 Trial & Error 방식에 의한 연구와 기업 Know-How라는 장벽에 부딪쳐 그 이론의 정립은 초보단계에 있다고 해도 과언이 아니다.
Spray Drying 공정에 있어서 Binder System 의 설계라는 관점과 Slurry-과립-성형체 및 소결체 특성의 인과관계 정립이라는 관점에서 더 많은 연구가 필요하리라 생각된다.
요업재료의 과학과 기술 Vol.8 (3) 1993